The most economical method of removing water from synthetic rubber is a mechanical screw press like the Expeller.
Anderson’s Moisture Expeller press was invented to provide processors with a new technology for separating process moisture from fresh crumb rubber (synthetic or natural). The continuous process “squeezes” the compressible rubber by means of a rotating interrupted screw, adjustable cylindrical elongated barrel with drainage bars, and an adjustable discharge mechanism, thus permitting the noncompressible water to flow from the process to water recovery systems. The crumb rubber containing 40‐60% moisture at feed is effectively dewatered to 6 to 15% water by weight at discharge. The discharging dewatered crumb is then fed to the inlet hopper of Anderson’s Expander/Dryer®.
Highlights
- Most widely used and economically feasible means of separating process moisture from crumb rubber
- Expeller models designed for capacities (dry base) from 100kg/hr. to 12,0000kg/hr
- This technology is used by virtually all major synthetic rubber producers for producing commodity rubber types such as polybutadiene and styrene‐butadiene rubber
- High‐efficiency conversion of torque to work in the “squeezing” process
- Anderson’s staff of process experts can offer unparalleled processing support to users based on hundreds of operating installations
Features
- Anderson manufactured reducer/thrust cases
- Standard 316 stainless steel materials in the process flow with availability of high‐alloy materials for corrosive processes
- Connected power from 25 HP (18.65kW) to 1,250 HP (930kW)
- Remote control of the process with Anderson’s PLC control panel
- Control features include:
- Adjustable die cross section
- Main worm shaft screw speed
- Barrel temperature
Applications
- All types of synthetic crumb rubber, natural rubber, reclaim rubber, block copolymers and most all non‐vulcanized elastomers
- Used to produce crumb rubber that is suitable for finish drying in downstream mechanical drying extruders or thermal dryers
- Will not change the molecular properties of the polymer
Shown here: Anderson No. 88c Expeller Press
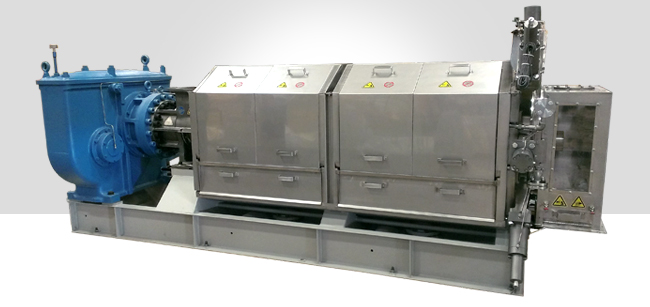
Shown here: Anderson No. 7 Expeller Press
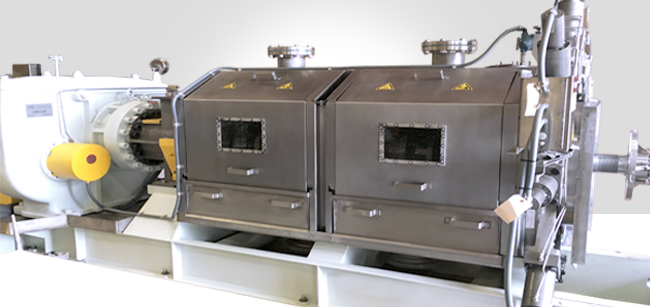
Shown here: Anderson No. 6 Expeller Press
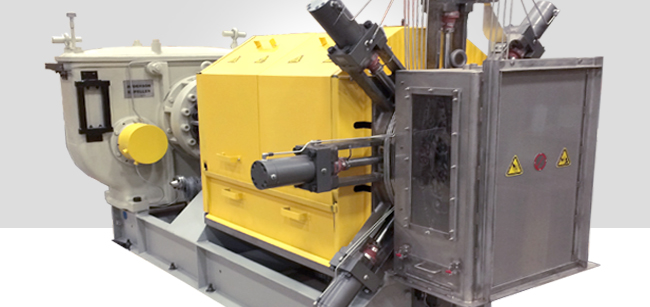
Expeller® and Expander-Dryer® are registered trademarks of Anderson International Corp.
Model | Max Con. Power | Max Capacity (Kg/Hour) | Moisture Specifications |
---|---|---|---|
Model No. 6 Expeller Press | 75 HP (56 kW) | 800 | 60% - 40% in, 15% - 6% out. |
Model No. 88 Expeller Press | 75 HP (56 kW) | 1,000 | 60% - 40% in, 15% - 6% out. |
No. 6/6B Expeller Press | 300 HP (224 kW) | 4,000 - 6,000 | 60% - 40% in, 15% - 6% out. |
No. 7 Expeller Press | 400 HP (300 kW) | 7,000 | 60% - 40% in, 15% - 6% out. |
No. 7A Expeller Press | 1,250 HP (930 kW) | 8,000 | 60% - 40% in, 15% - 6% out. |
No. 88C ExpellerPress | 490 HP (366 kW) | 8,000 - 10,000 | 60% - 40% in, 15% - 6% out. |
No. 88 Expeller Press | 1,250 HP (930 kW) | 12,000 | 60% - 40% in, 15% - 6% out. |