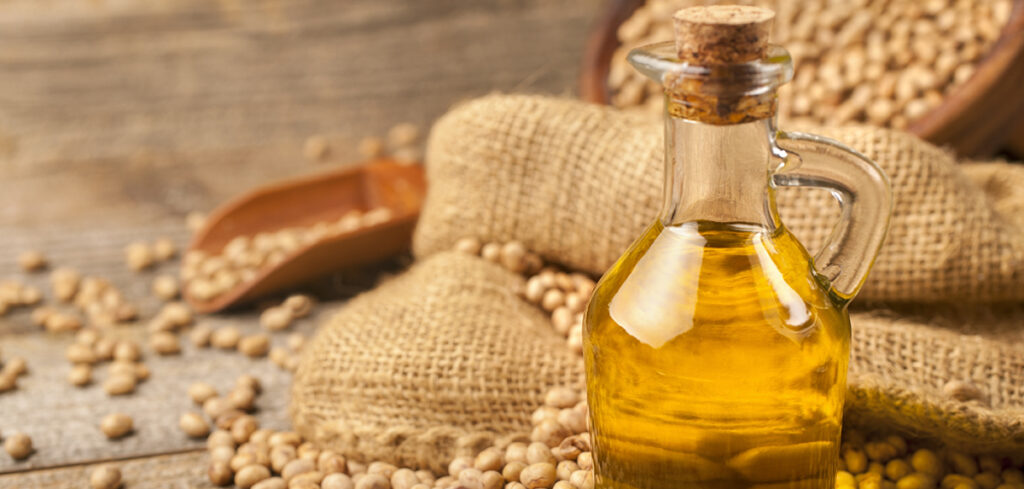
The original oil expeller press was invented in the late 1800s by Anderson International’s founder, Valerius D. Anderson. This patented mechanical screw press design was a radical departure from hydraulic presses used at the time. The Anderson expeller’s primary advantage was that it allowed for continuous oil extraction and the processing of large quantities of materials with minimal labor. Since then, though the technology remains largely the same, continuous improvements in the materials of construction extend the life of wearing parts, and the increased scale of the machines delivers much greater capacity.
Continually striving to improve efficiency and durability, and produce the highest quality equipment on the market, Anderson released its latest expeller presses in 2018.
The new Anderson Oil Expeller® line, designed for soybean, canola, sunflower, copra, and numerous other oilseed extraction, has proven lower operating and maintenance costs than other presses available today. It adapts easily to different finished products and operating speed requirements. And when paired with extrusion technology, it can reduce oil residuals to as low as five percent in the meal at six tons per hour.
Here are seven features to know about the new oil expeller press.
Features of the oil expeller press
(1) Gearbox with v-belt motor coupling
The expeller is fitted with a standard design helical gearbox that is available commercially, enabling quick part replacement and servicing. The gearbox is coupled directly to the motor by a small v-belt which provides a built-in failsafe. During an unexpected jam in the machine, the v-belt will slip or make noise instead of continuing to engage, preventing costly damage.
The v-belt also allows for easy adjustment of motor speed and cuts costs for processors who do not want to invest in a variable frequency drive.
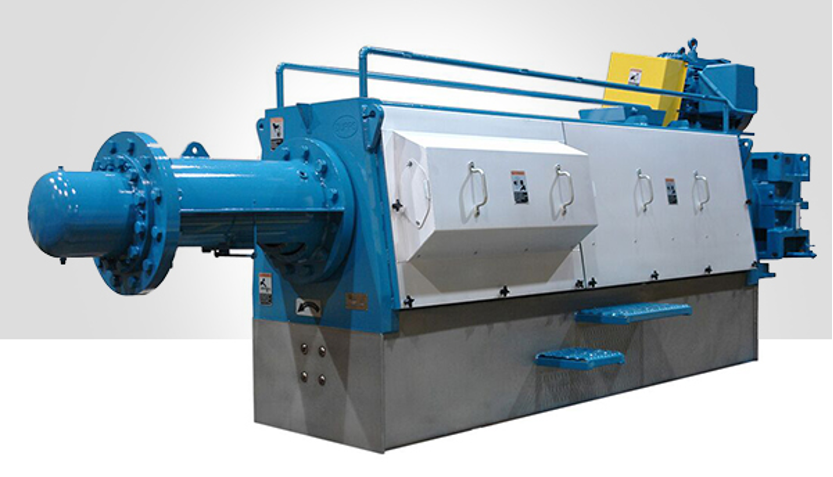
(2) Reversible thrust unit
The machine boasts an independent thrust unit that allows for movement in both directions. When the expeller jams, a processor can clear the obstruction by reversing the machine instead of opening and disassembling it. A simple reverse of the motor can break up the clog and reduce downtime by several hours every time.
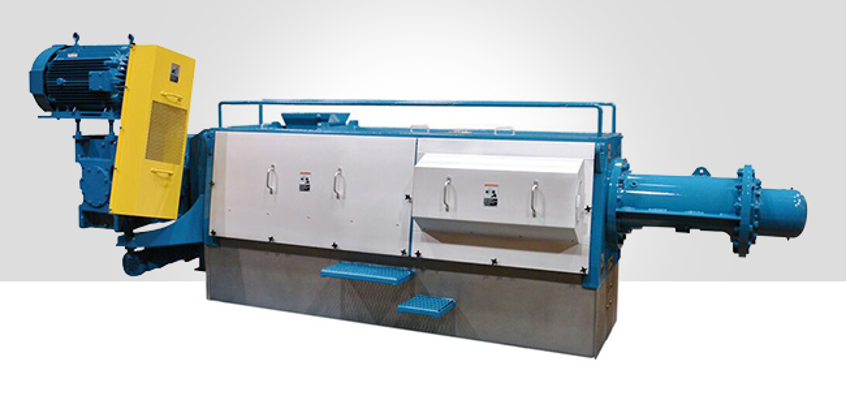
(3) Feed hopper with drainage capabilities
Excessive oiling can clog an expeller if it floods the feed section. The inlet feed hopper is built with a drainage section to prevent plugging due to oil migrating backward.
(4) Main drainage cage
The main drainage cage is six sections long and, when combined with the feed hopper, provides over 80 inches of drainage. Because each section is independent, spacing is adjustable throughout the machine. Reducing spacing as pressure increases in the machine will reduce the number of fines in the oil and increase overall efficiency.
The frame is built from cast iron, making it durable and able to stand up to the high pressure needed for efficient oil separation.
(5) Main worm shaft
The main worm shaft has segmented flights that are a patented dual cast worm. The manufacturing process dual casts the base metal with the hard-facing cast directly on top. The unique process allows for thicker hard facing parts that are more uniform, at a lower cost than labor-intensive and expensive conventional methods.
(6) Hydraulic choke
The press has a hydraulically operated choke that makes the backpressure applied to the material adjustable. By simply setting the pressure, the choke will adjust based on how the press is running. This flexibility allows processors to extend the life of their parts as the barrel and shaft tolerances inevitably widen due to wear. An auto-release function opens up the machine when it begins to plug, de-escalating high-stress situations.
(7) Built-in jib crane
A 360-degree rotating crane is built into the structure of the press. It allows lifting and removal of the press’s heavy components without the additional expense of overhead rigging. This feature is unique in the market and essential for reducing downtime during maintenance.
Need assistance with your oilseed equipment now?
Do not hesitate to call us at 1(800) 336-4730 or use our contact form.
Increased efficiency with the right upstream equipment
Contributing to the new oil expeller press’s high performance is the option to connect it to high-quality extrusion equipment upstream. The expeller is perfectly paired for the Anderson 12″ Dox Extruder, the largest dry extruder for soybean on the market. The Dox replaces expensive drying equipment to efficiently break down, shear, and cook the oilseed in one simple step.
Installing a Dox ahead of an expeller doubles the press’s capacity and doubles the life of pressing parts. When paired, the system can press over 100 metric tons per day with residuals as low as five percent.
Read more: High-Shear Extruder Adds Extreme Flexibility For Soybean Oil Milling
An investment that saves money
Investing in a high-quality expeller with a carefully planned design will save processors money in the long run from reduced downtime and increased oil recovery and efficiency. Anderson has a long history of building machines and parts that last. In fact, Anderson machines installed in the 1920s are still running today. The expeller and high-shear extruder system are a reliable, cost-effective investment and will last for decades to come.
For a same-day quote on the Anderson oil expeller press with a high-shear extrusion system, contact us here.