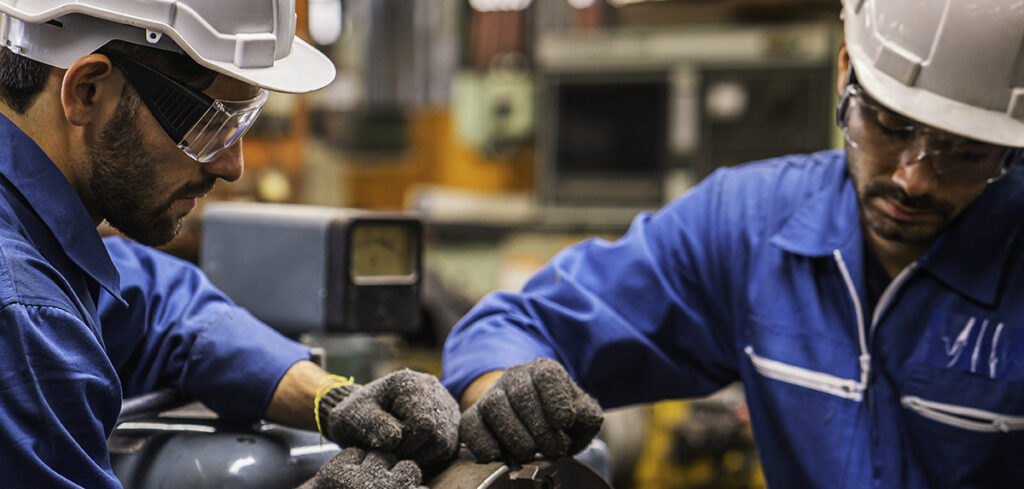
Downtime in oilseed crushing plants can wreak havoc on production standards. According to a recent survey, oilseed manufacturers lose an average of 5% productivity and as much as 20% due to downtime. When it comes to unplanned downtime, oilseed processors cite unexpected equipment failure as the most common reason, followed by process failures and human error.
Regular maintenance of machines helps manufacturers detect minor problems early before oilseed equipment failure. On extruder machines, routine maintenance includes inspection, lubricating parts, and replacing worn contact parts. Smart manufacturers follow best practices for regular maintenance to prevent costly unplanned downtime.
Maintenance of the extruder drive system
The drive system in a high-shear extruder requires regular maintenance to keep the machine running. If a part goes down in the drive system, the entire machine is down until the operator can replace the part. The drive system on the Anderson International Dox Extruder is comprised of the gearbox, thrust unit, and direct or v-belt drive.
The gearbox and thrust unit should always be well lubricated and kept at a stable, cool temperature. On oilseed extruders, the gearbox and thrust units are encased in oil in a lube system to achieve lubrication and temperature requirements. Depending on the machine, the drive system’s components may be housed in a separate or a combined lube system. Daily monitoring is essential to ensure sufficient oil levels and stable temperature. A temperature spike indicates either a damaged part or the machine is low on oil. Anderson’s Dox Extruder is equipped with an oil level indicator and instruments to monitor internal temperature.
Oilseed processors must flush out the lube system oil every six months to one year, replace the filter, and refill the oil. Gear inspection should be performed to look for pitting and metal contaminants in the oil to identify grinding or gear misalignment issues. Additionally, operators with v-belt driven extruders need to perform daily inspection and maintenance. The v-belt should be monitored for fraying and abnormal sounds such as squealing. These inspections will identify signs of worn-out parts that need to be replaced before failure.
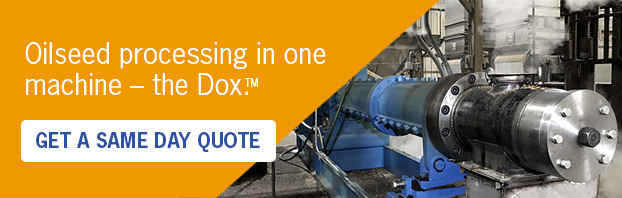
Maintenance in the working components
Even an extruder built with the highest-quality steel will eventually show signs of wear due to the abrasive nature of oilseed under pressure. The most susceptible areas for wear are at the choke and discharge, where pressure is highest. The inlet, where pressure is minimal, is impacted less by the abrasive oilseed.
One indication of wearing parts is when an operator notices a change in the performance of the extruder. The change may be visible, or the operator may use a more reliable monitoring method by tracking motor load. As tolerances open up due to wear, the amp load of the motor will drop. When no process adjustments are made to address the changes – like a choke adjustment or change in product type or capacity – and the operator identifies a steady drop in the motor’s amperage, it is time for maintenance.
Even without visible signs of wear or documented changes in amp load, planned downtime for maintenance is critical, and operators should schedule it regularly throughout the year. How often this occurs depends on the conditions of operation. Extruders that operate 24/7 will require maintenance every three to four months, while for most processors, wear begins impacting their machines at around four to five months. Low-quality seeds or poor preparation upstream may also shorten the length of time between maintenance activities.
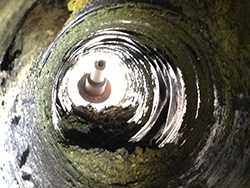
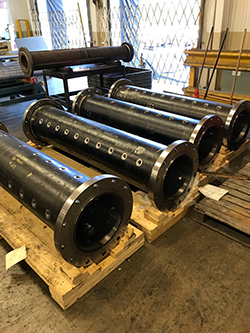
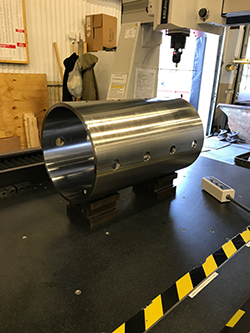
Proactive extruder machine maintenance
Proactively scheduling maintenance will ensure that wear is caught early and save a processing facility from machine failure and costly repairs later. Standard wearing parts such as the choke inserts, worm segment liners, and breaker screws can be removed and replaced more quickly and easily than, say, the entire choke. But when worn parts are left long enough, the damage can extend beyond the contact parts and require a heftier repair.
Need assistance with your oilseed equipment now?
Do not hesitate to call us at 1(800) 336-4730 or use our contact form.
In one client case in the midwestern US, a large-scale processor’s failure to keep up with maintenance left them in a precarious situation. Anderson process and maintenance experts received their extruder for repair after a rogue piece of metal entered the machine and destroyed it. Upon inspection, the Anderson team could see the breaker screws were worn down and thin. Breaker screws are highly susceptible to snapping when worn, and the operator could have addressed this issue if the extruder was proactively maintained. Although the rogue metal may have entered with the product, it was only a matter of time before this machine met its fate.
“Get in the habit of proactively looking at your machine,” says Eric Stibora, Vice President of Sales and Marketing and Anderson International. “Don’t wait for a catastrophic failure.”
A sudden failure in the machine means a loss in production, capacity, and wasted labor expenses, not to mention the added stress it places on the facility. While planned maintenance also comes at a cost, it reduces loss because it allows for proper inventory planning, staffing, and expediated repair time. Time is money, so reducing downtime length is critical. Planned maintenance, adequate spare parts, and proper plant layout are vital components to minimize costly downtime.
Additionally, proper maintenance ensures maximum efficiency of the extruder machine and processes downstream. If an extruder does not perform properly, it ultimately hurts the ability to generate oil efficiently, and profitability will drop.
Maintenance training with industry experts
Keeping up on best maintenance practices can be challenging, especially in facilities with numerous machine types or experiencing staff turnover. As part of its field services, Anderson International delivers on-site maintenance training to clients. “We want to educate our clients on all aspects of the process. One of the most important elements for success is performing proper maintenance on the machines we provide to them,” says Stibora. “We believe that if our clients are successful, we are successful.”
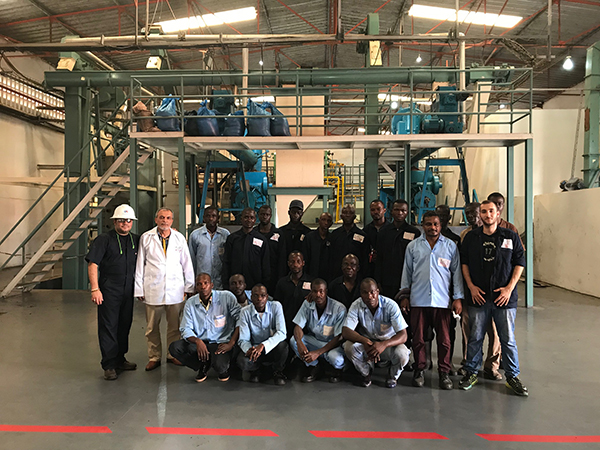
Anderson engineers have worked on over 12,000 units, 1,000 plant installations in over 100 countries, and they have witnessed the pitfalls of poor maintenance. Proper care of Anderson’s systems and the entire process is the number one reason Anderson installations from the 1920s are still in operation today.
For more information about the Dox Extruder or on-site maintenance training at your facility, contact an Anderson International expert today.