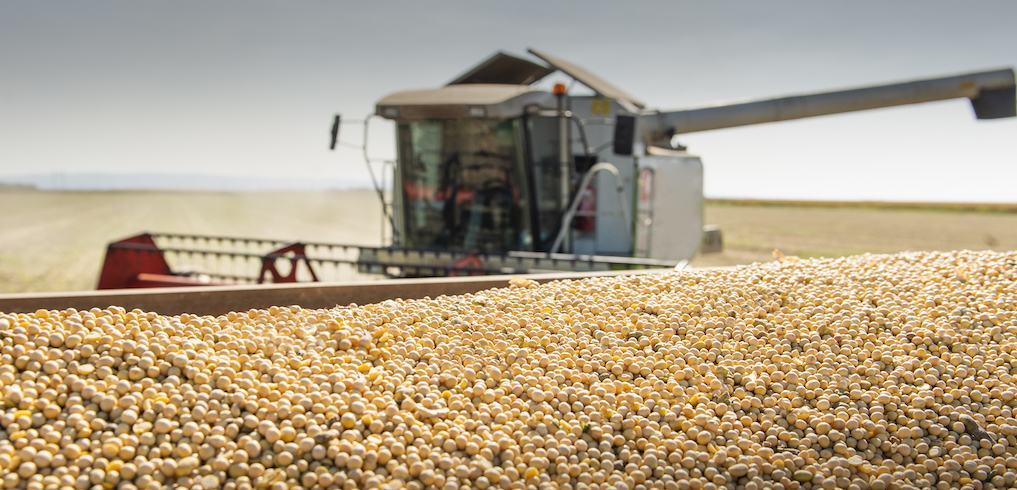
Driven by the search for more renewable energy sources, U.S. biofuel production continues to expand. As the demand for biofuel increases, so does the demand for soybean oil—which generates more than 60% of the vegetable oil-derived biodiesel currently produced in the U.S. Biofuel production has rippling effects throughout the agricultural supply chain, so it’s important to understand the potential market for soybean biodiesel.
Although soybeans are primarily grown in the U.S. to produce high-protein meal for livestock feed, the oil continues to grow in value as well. In fact, the biodiesel demand for soybean oil has increased 300% in the last decade.
Below, we’ll explore the current trends in biodiesel and compare soybean oil extraction methods to evaluate soy’s opportunities in the biofuel industry.
Biodiesel outlook
In 2020, the U.S. produced approximately 11.57 million metric tons (MT) of soybean oil. About 3.9 million MT of this supply was processed into soybean biodiesel, while another 1 million MT were exported.
Energy industry analysts expect the domestic production of biodiesel to quadruple between 2020 and 2022, surging from about 550 million gallons (or 1.6 billion MT) to 2 billion gallons. To keep pace with this anticipated expansion, domestic feedstock producers must ramp up capacity and add several million MT of soybean oil to their annual production totals.
Earlier this year, soybean oil prices hit 12-year highs that outpaced the price of soybean meal. The value of soybean oil, relative to the total margin of crushed soybean stock, increased from 35% to nearly 45% as a result, according to the U.S. Soybean Export Council.
Although the increased production of soybean biodiesel will heighten the demand and price for soybean oil, soy meal prices will head in the opposite direction. As more soybeans are processed to supply oil for biodiesel, the price of meal will naturally fall—potentially lowering feed costs for farmers. Meanwhile, as soy oil use for biodiesel increases, its use in food applications will likely decline as consumers substitute other vegetable oils like palm and canola instead.
While this growing demand for soybean biodiesel highlights the potential for plants to ease U.S. dependence on crude oil, it also raises questions about soybean oil production and processing capacity.
Soybean biodiesel production
The two most popular methods for recovering oil from soybeans are chemical extraction with a solvent and mechanical extraction with a screw press. Both of these methods can be used to process soy for the biodiesel market.
Mechanical extraction uses brute force to squeeze oil out of the seeds, resulting in about 80-95% oil recovery. The most efficient process starts with high-shear dry extrusion to prepare the soybeans for extraction. A machine like the Anderson Dox™ Extruder cooks, dries, and sheers the oilseeds to deactivate harmful enzymes and prepare the proteins for more efficient pressing.
Then, prepared oilseeds enter a screw press, like the Anderson Oil Expeller®, where friction and pressure compress the seed material to separate the fats from the solids.
The benefits of mechanical extraction include:
• Lower investment costs, ideal for plants processing less than 1,000 tons per day.
• Chemical-free processing, ideal for higher value products and safety.
• Less complicated process, although oil losses are higher (around 5-8%).
Solvent extraction washes flaked soybean with a hot solvent like hexane to dissolve the oil from the meal. This creates two byproducts—the oil/solvent combination called the miscella, and the combination of wet meal and solvent known as the marc—which are further treated to remove the remaining hexane.
Just as the Dox Extruder prepares seeds for the Expeller, an expander like the Anderson Solvex™ prepares soybeans for solvent extraction. Unlike the Dox, which generates heat through friction, the Solvex uses steam-generated heat to cook the oilseeds. A sudden drop in pressure causes this moisture in the seeds to expand, creating a porous material known as soybean collets, which can be extracted more efficiently.
The benefits of solvent extraction include:
• Higher oil recovery, leaving less than 1% residual oil behind.
• Higher capacity, ideal for plants that process more than 1,000 tons per day.
After extraction, soybean oil is converted into biodiesel through a chemical process called transesterification. The resulting fuel is then blended with petroleum diesel—most often sold as a 5% mix, although some trucks can use up to a 20% biodiesel blend known as B20.
Need assistance with your oilseed equipment now?
Do not hesitate to call us at 1(800) 336-4730 or use our contact form.
How soybean biodiesel stacks up
The production of biodiesel requires less energy and results in lower emissions compared to fossil fuels. When it comes to performance, biofuel is closely on par with petroleum diesel in terms of fuel economy, horsepower, and torque—and it even offers some advantages like enhanced lubrication, which can extend engine life.
With these potential benefits, renewable fuels like soybean biodiesel can help reduce the country’s dependence on fossil fuels, while lowering the cost of soy meal for livestock producers. As state carbon policies and widespread energy concerns continue to drive biodiesel demand, soybean oil could create more value for soybean farmers seeking alternative markets for their product.
To learn more about extracting soybean oil for the biodiesel market, contact the processing experts at Anderson International.