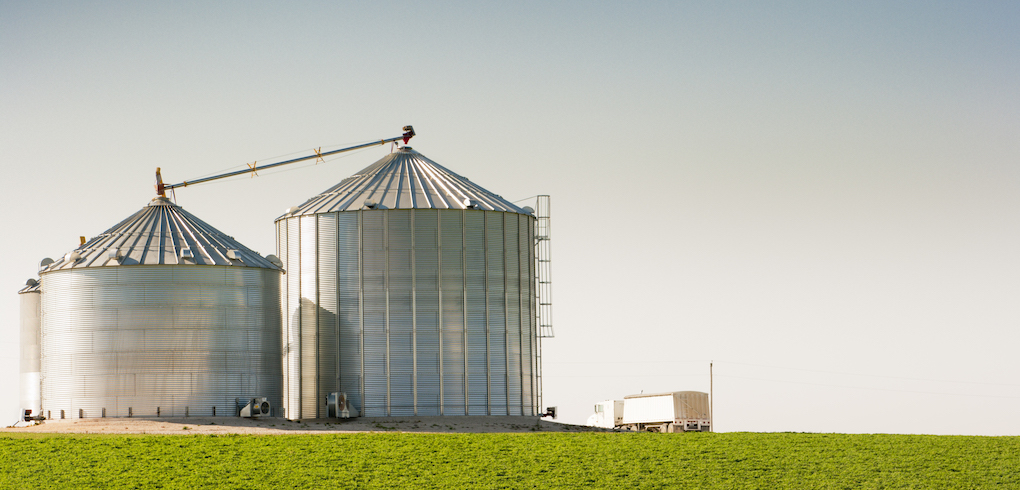
The first step to successful soybean processing begins long before any oilseeds even enter your plant. Ensuring sufficient storage prior to processing can literally make or break your operation. It’s imperative that processors consider properly sized and sorted soybean storage bins from the start.
For any oilseed processor, maximizing uptime and minimizing downtime is a critical balancing act. Since most systems are designed to run 24/7, proper storage can be key to ensuring that you have enough product available for continuous processing. For this reason, reliable storage can help processors ride out the waves of market volatility by allowing you to stock up on soybeans when the price is right.
However, improperly stored soybeans can be detrimental to a processing operation. Poor storage can promote mold growth and soybean spoilage. This results in reduced performance and efficiency of your expeller and ultimately decreases the quality of the extracted oil.
Read More: Sequence of Operations is Critical for Oilseed Processing
Set up your processing facility for success with this checklist for effective soybean storage bins.
Proper storage can be the solution to this supply dilemma, but only if you size your soybean storage bins according to the size of your operation, the schedule of how often you receive fresh shipments to your facility, and the quality of the raw product you accept. All of these factors should be carefully considered when planning your soybean storage capacity.
Read more: Maximize Your Expeller-Pressed Oil Process with Overflow
Soybean moisture levels
Follow these tips to achieve the right moisture content, temperature, and airflow in your storage silos:
- Moisture content around 12-13% is adequate for soybeans during short-term winter storage. Cooler temperatures help maintain quality at those levels. But if you’re storing supplies long-term throughout the spring and summer, soybeans should be dried down to 11% moisture. This reduces the risks of mold and bacterial growth that accompany higher moisture levels over time.
- In a perfect season, soybeans may dry naturally in the field before harvest. But to counteract wet, cool fall weather or shortened growing seasons, supplemental heat may be required to sufficiently dry soybeans for storage. Processors should be very careful when drying soybeans. They are fragile and can be easily cracked and damaged by hot, dry air or rough handling.
- In a perfect season, soybeans may dry naturally in the field before harvest. But to counteract wet, cool fall weather or shortened growing seasons, supplemental heat may be required to sufficiently dry soybeans for storage. Processors should be very careful when drying soybeans. They are fragile and can be easily cracked and damaged by hot, dry air or rough handling.
- Cooling soybeans gradually as outdoor temperatures shift can help reduce moisture migration and condensation in the silo. To maintain the quality of your supply, most producers recommend that soybeans should be stored at temperatures between 35-40 degrees in the winter. It is also recommended to aerate in the spring so that temperatures never exceed 60 degrees.
- Proper airflow in your soybean storage bins is key to maintaining target moisture levels. Since soybeans have less airflow resistance than shelled corn, fans that are sized specifically for corn will produce greater airflow through soybeans, drying them even faster. To protect fragile soybeans during aeration, try to avoid high-friction systems that constantly stir or recirculate grain.
Regardless of how you dry or cool your crop, evaluate your soybean storage bins frequently—at least every two weeks during cold winter months—to ensure optimum quality and to identify potential issues before they cause unmanageable problems.
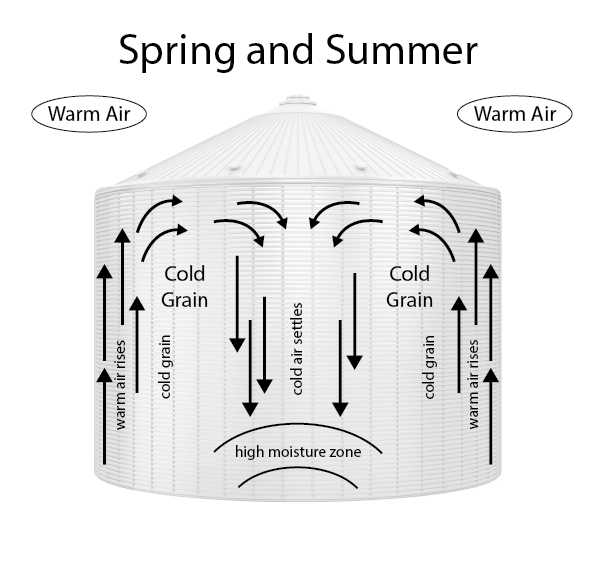
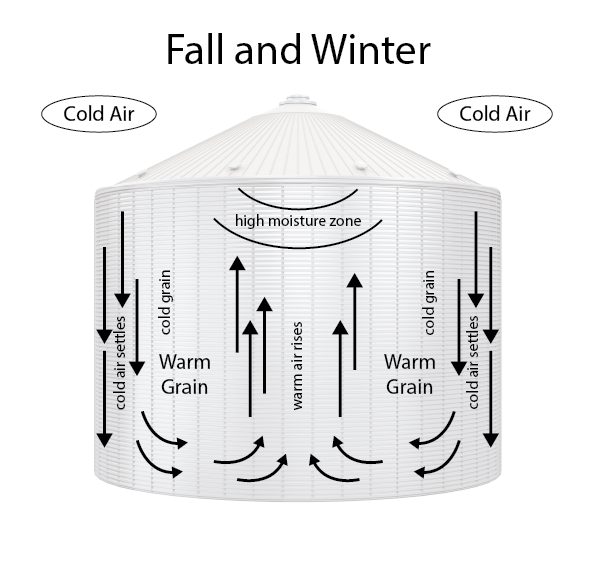
Read more: Critical Elements Behind Successful and Complete Processing Systems
Foreign material content
Carefully inspect your soybean deliveries before putting them into storage. This can ensure you’re not wasting precious storage space to house insects or other foreign materials that can degrade the quality of your oilseed. Like any process, if you put garbage in, you’ll get garbage out.
Consider cleaning your raw material with a “scalping” system. This system removes large, oversized particles such as pods, leaves, stems, and other debris. In the same way that one bad apple can spoil the whole bushel, one load of dirty soybeans can sully your entire storage bin. If you do accept lower-quality soybeans, make sure you dedicate a separate storage bin for each grade of product. Avoid mixing your clean supplies with foreign material.
Sampling soybean supplies can also help processors gauge the quality of oil they’ll produce. For example, if you’re accepting soybeans that have already been damaged by heat, frost, insects, or improper handling, the fat content of these soybeans may have already begun breaking down. You can’t reassemble these free fatty acids during processing. These poor qualities are going to carry through to your end products—resulting in lower oil yields and decreased quality.
Need assistance with your oilseed equipment now?
Do not hesitate to call us at 1(800) 336-4730 or use our contact form.
Optimize your soybean storage bins
Ultimately, the quality of soybeans that enter your processing plant will determine how efficiently your equipment functions. If your storage infrastructure is designed to maintain proper moisture levels, ideal temperatures, and the absence of foreign materials, your silos can help facilitate the highest quality soybean supplies. The result is more efficient processing by the time your crop heads to the oil expeller.
If, on the other hand, your soybean storage bins allow high moisture levels, poor quality materials, and less-than-perfect conditions that invite insects, mold, and fungi to degrade your supply, then your products will suffer.
Maximizing your soybean crush margins begins with proper soybean storage bins. Having a plan to inspect, sort, handle, and store your soybeans appropriately can set your processing plant up for success while securing top value for your products.
Contact Anderson International to learn more about getting the best results with your oilseed processing system.