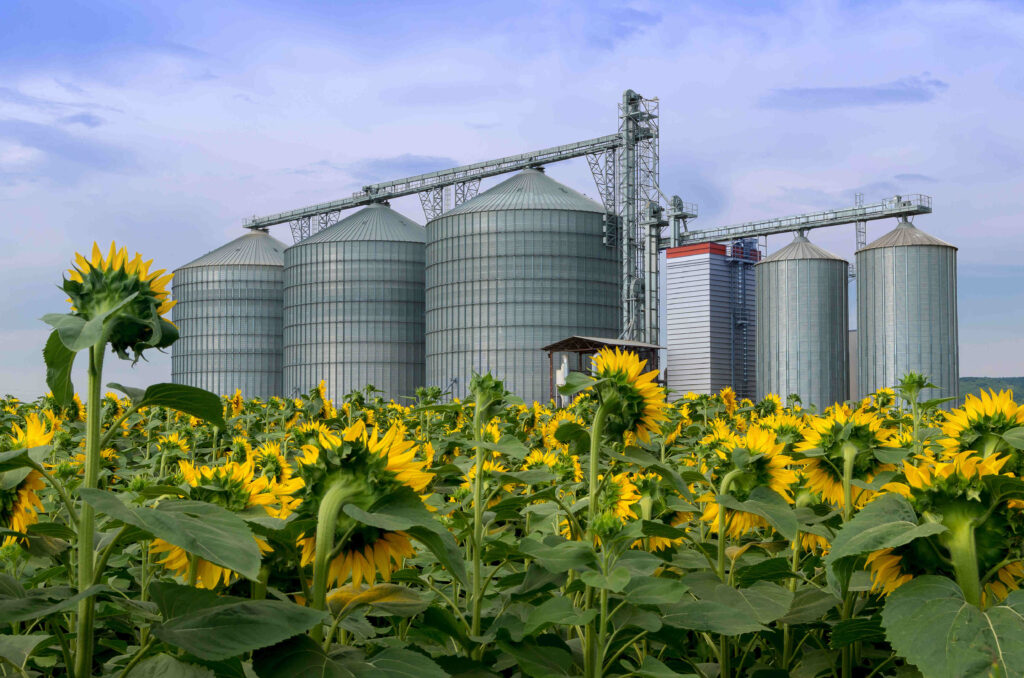
Sunflowers provide the third-largest source of protein for livestock diets and U.S. oilseed production. To capitalize on this supply of U.S. sunflower to produce valuable feed ingredients for farms throughout the region, Wyoming-based 307 Processing set out to build a new sunflower seed processing plant.
Owners Joel and Curtis Hjorth saw an opportunity to tap into the growth potential of sunflower seeds. This year, domestic sunflower crush is expected to reach 1.32 billion pounds, with sunflower oil consumption rising to 735 million pounds and sunflower seed meal usage expanding to 694 million pounds. Building a state-of-the-art sunflower processing plant positioned 307 to meet the increasing demand.
Here’s how Anderson International partnered with 307 Processing to design and build a facility capable of crushing local sunflower seeds to produce high-quality oil and meal.
Challenges and opportunities with sunflower seed meal
Sunflower seed meal supplies a valuable source of protein, fiber, and energy to supplement the diets of beef cattle and other livestock. Most U.S. sunflower oilseed is produced in North and South Dakota, in close proximity to many livestock farms and ranches that need these beneficial feed ingredients. Naturally, 307 Processing saw an opportunity to connect the dots with a new sunflower seed processing plant.
However, crushing raw sunflower seeds to separate the oil from the meal requires the right processing equipment and systems to preserve the quality of both byproducts. Sunflower seeds are difficult to crush because of their tough outer shells and high fat content of more than 40% oil—compared to soybeans, which average about 18%. Most standard equipment to press soybeans isn’t best suited to press seeds containing that much fat.
To overcome these challenges, Joel and Curtis knew they needed the best oilseed processing equipment to efficiently crush high-oleic sunflower seeds at their plant. They turned to Anderson International, leveraging the company’s deep oilseed extraction expertise to design the most efficient processing system with the capacity to crush up to 50 tons per day.
Download our case study about 307 Processing’s new mechanical sunflower processing plant
The solution: Anderson conditioner and extruder
The Anderson Oilseed Division Team of Sales, Project Management, and Engineering worked closely with 307 Processing and their general contractor to design a mechanical sunflower seed processing plant in Gillette, Wyoming. After months of collaborative planning to develop conceptual, preliminary, and final designs, the facility began to take shape.
The new 307 sunflower processing plant features several strategic steps designed to optimize sunflower seed meal and oil production, including:
- Inspection and storage
- Locally sourced high oleic sunflower seeds are received and inspected to start the process. The quality of raw sunflower seeds directly correlates to the profitability and operational efficiency of the plant. Proper storage conditions preserve the quality of these raw materials until the seeds are crushed.
- Seed cleaning
- The sunflower seeds are conveyed from storage to a cleaner that removes debris like sticks, stones, dirt, and other foreign material that could damage the processing equipment and contaminate the products.
- Conditioning
- Clean sunflower seeds are ready for conditioning. The process of conditioning oilseeds with steam heat prepares the material for pressing by breaking down the seeds and lowering the oil’s viscosity so it flows more freely. The conditioning process also helps denature proteins and deactivate fat-splitting enzymes, while ensuring sunflower seeds leave the conditioner at a consistent temperature and moisture level.
- Dry extrusion
- Then, cleaned, dried, and conditioned sunflower seeds are fed through the Anderson Dox™ 800 Extruder, which uses mechanical energy to quickly cook, dry, and shear oilseeds to prepare them for pressing. The high-shear action inside the extruder ruptures the oil-bearing seed cells while generating frictional heat. This works like a pressure cooker to quickly deactivate harmful enzymes without degrading the quality of the proteins, while pre-pressing fat from the oil-rich seeds.
- Mechanical pressing
- Sunflower oil is extracted in both the extruder and the screw press to recover as much oil as possible from these high-fat seeds. Like the extruder, the screw press uses mechanical force to squeeze liquid oil from the seeds, creating frictional heat and high pressure to help separate the fats from the solids. The pressed sunflower seed meal is cooled and ground in a hammermill to meet the requirements of 307’s customers, while the sunflower oil undergoes additional screening and clarification before it is stored for sale.
While the new sunflower seed processing plant was being commissioned, the Anderson Oilseed Division Team and its Anderson Vendor Partners provided hands-on training to 307’s team, ensuring a smooth hand-off as the facility prepared to open.
The results at 307’s new sunflower seed processing plant
Over about one year, Anderson helped bring 307’s vision to fruition through its new mechanical sunflower processing plant. Equipped with one Anderson Conditioner, one Dox 800 Extruder capable of crushing 2 tons of sunflower seed per hour, and one 6” expeller press, the plant has the capacity to process 50 tons of oilseed per day.
The facility will be able to add 50% more capacity in the future, which gives 307 Processing room to grow. Although initially focused on sunflower seed processing, the plant is also poised to crush flax, canola, and other oil-rich seeds as well, providing 307 with the flexibility to expand.
Using industry-leading equipment from Anderson International, along with proven best practices in specialty oilseed handling, conditioning, extrusion, and pressing, 307 Processing has exceeded its initial expectations. On average, the sunflower seed meal produced by 307 contains residual oil levels between 6-8%, below the company’s original target of 8% RO. This consistent quality output allowed the processor to launch and sell a proprietary line of expeller-pressed sunflower seed meal along with sunflower oil to supply animal feed producers throughout the region.
Anderson’s high-shear dry extruder provides best-in-class oil recovery and meal nutrition with the lowest energy usage, at less than 75 kilowatt-hours per ton of sunflower seed processed. Installing a Dox Extruder upstream of the expeller doubles the capacity of the press and the life of the pressing parts at 307’s sunflower seed processing plant, while reducing energy costs and improving oil recovery rates. This equates to the lowest total cost of ownership, as measured by uptime tonnage produced and energy consumed—positioning 307 Processing for maximum profits as they capitalize on the expanding market for sunflower seed meal.
Contact us to learn more about the mechanical crushing capabilities of Anderson’s oilseed processing equipment.