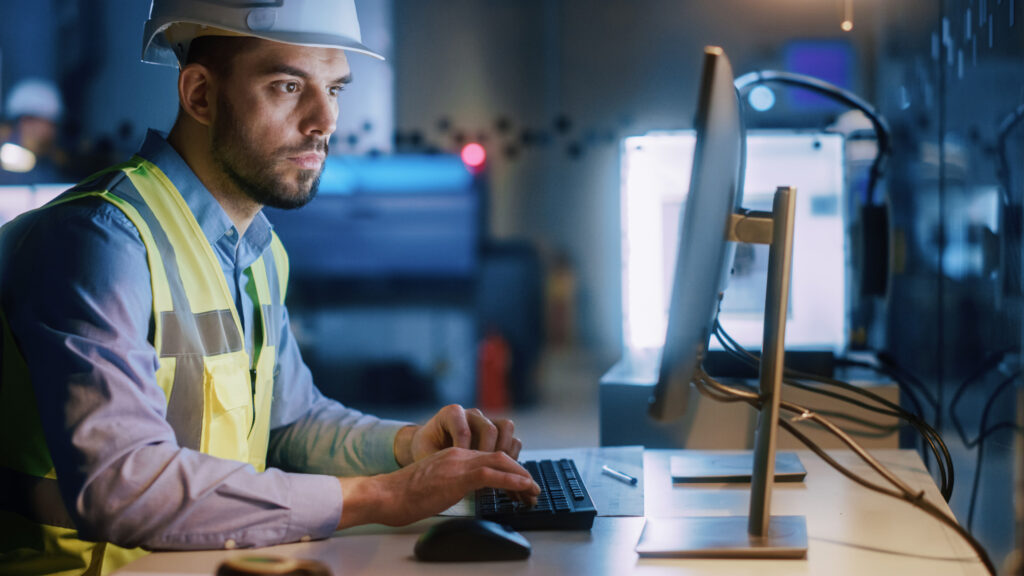
The day-to-day operating costs involved in crushing oilseeds can make or break the profitability of a mechanical processing plant. To combat tight margins and fluctuating market prices, processors must operate their facilities as efficiently and cost-effectively as possible—which requires a keen understanding of their operating expenses in terms of cost per ton for soybean oil production.
Whether you are estimating the potential return on investment (ROI) for new oil mill machinery or simply analyzing the efficiency of your existing system, understanding how to calculate your plant’s operating costs is crucial to your bottom line. To achieve the best possible margins, you must understand how much it costs to crush one ton of soybeans.
When calculating cost per ton, soybean oil plants must consider all the operating expenses required to run their mill. The average mechanical oilseed processing plant’s largest operating costs typically include energy consumption, equipment maintenance, and labor costs.
Important operating expenses to consider
- Energy consumption
Traditional processing equipment is notoriously inefficient and expensive, using costly steam utilities and industrial boiler systems to power multiple machines. Switching to more efficient equipment designed to consume less energy can drastically reduce your utility bills and overall operating costs.
For example, the Anderson Dox Extruder eliminates the need for separate flaking mills, steam heating, and stacked cooking and drying vessels by combining multiple processes into one multifunctional machine. Using mechanical energy to generate heat instead of relying on steam, the Dox Extruder consumes less energy per ton than any other extruder on the market, controlling the overall cost per ton for soybean oil production.
- Equipment maintenance
Maintenance costs are unavoidable in mechanical oilseed processing plants. Even the most durable machines require regular upkeep to maintain peak performance. The key is developing proactive routines for both expeller maintenance and extruder maintenance to prevent unexpected breakdowns and expensive repairs—avoiding the costly downtime those can cause.
While some compact extruders require a rebuild every three or four weeks, the Dox Extruder is engineered to last six months before rebuilding, thanks to its rugged construction and durable design. Although this equipment requires a higher capital investment upfront, Anderson’s machines save processors money over time through longer lifespans and less frequent maintenance.
- Labor costs
Employee wages comprise another essential operating expense at mechanical processing plants. Ongoing labor shortages and increasing wages can make these costs challenging to manage.
One important aspect of managing labor costs is employee productivity. A well-trained workforce is essential to keeping an oilseed processing plant running as smoothly, safely, and efficiently as possible, ultimately impacting profit margins and other measures that comprise cost per ton.
How to calculate cost per ton for soybean oil producers
Operating expenses are just one piece of the equation when calculating cost per ton for soybean oil production. In addition to operational expenses, processors must also consider the profit margins of their crushing operation. The “crush margin” measures the value of the oil and meal extracted from one bushel of beans minus the cost of raw materials.
For a sample calculation of crush margins at an average mechanical processing plant, download Anderson’s guide to soybean processing costs. Generally, since the soybean crush margin indicates your potential profits per bushel (or ton) and your operating expenses reveal how much you spend to process one ton, you must maintain production costs lower than your crush margin to turn a profit.
soybean crush margin – operating costs = cost per ton
The key to controlling this equation is to extract as much high-quality oil as efficiently as possible, boosting your crush margin while driving down your operating costs. The Dox Extruder swings this balance in your favor by optimizing your plant’s overall efficiency. By combining multiple production steps into one efficient machine, the Dox cuts energy usage, doubles the capacity of the downstream press, and doubles the life of the pressing parts to minimize operating costs while maximizing profits.
Investing in long-term value
Processing machines with small price tags might initially seem appealing to the cost-conscious processor. Still, you must weigh the initial capital investment against the operating expenses over time to accurately calculate the cost per ton. Operating costs can negate your savings if your energy-draining equipment requires frequent rebuilds and repairs, resulting in extended downtime.
On the other hand, investing in high-quality oil mill machinery from Anderson can save your operation money over the long run by keeping maintenance costs, energy bills, and other production expenses in check. Additionally, Anderson’s oil extraction experts can provide ongoing service and support to optimize the efficiency and profitability of your processing plant.
Contact us today to maximize your soybean oil plant’s crush margins, lower operating expenses, and achieve the ideal cost per ton.