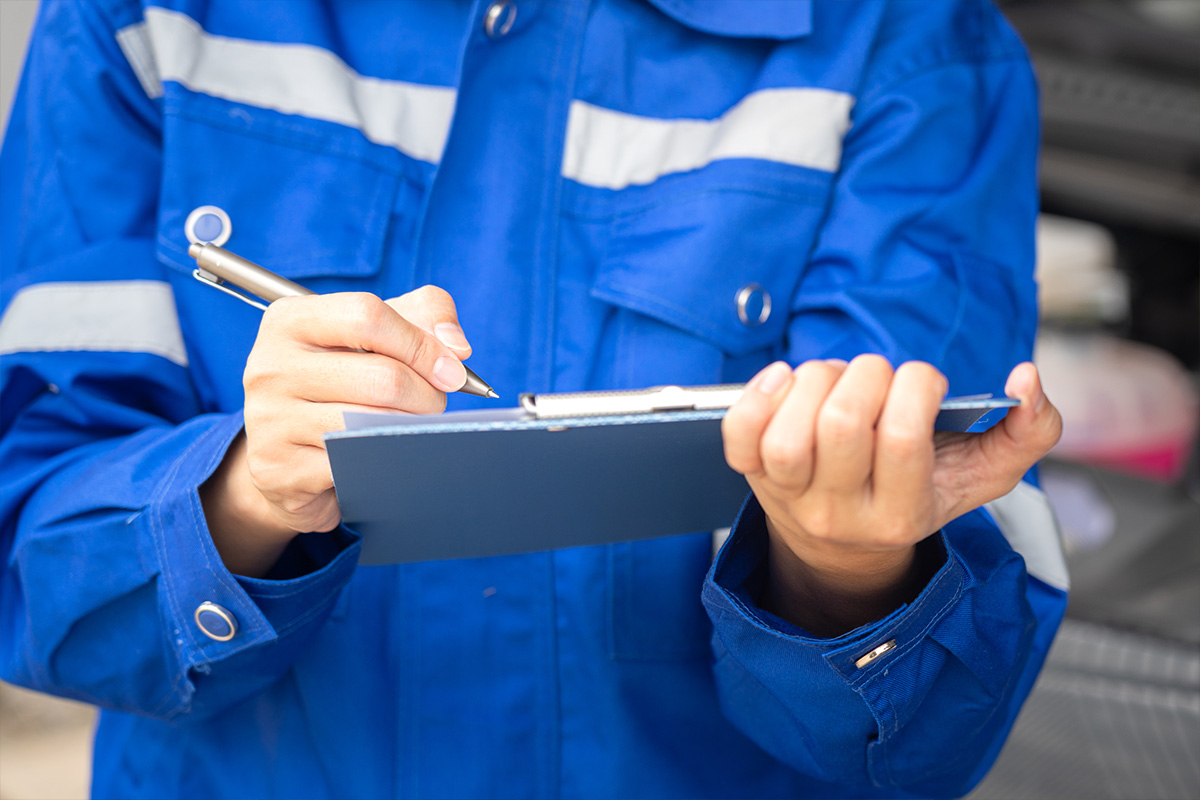
Regular maintenance is the key to keeping oilseed processing equipment running smoothly. Facilities can set themselves up for success with accurate, updated records that detail each inspection and every repair over the lifespan of your machinery. Equipment maintenance records are critical to tracking machine performance over time, preventing unexpected breakdowns and unplanned downtime, and avoiding all the headaches that come with these unfortunate events.
Relying entirely on your technicians’ memory to recall when inspections and repairs were last performed and expecting them to remember when it’s time to service each machine again can lead to disaster. They might forget to check the lubrication oil levels in the gearbox until they notice the equipment overheating because the gears are grinding each other down. Or they might not replace worn flighting in the oil decanter until clients report excessive solids in your product.
Keeping a log of maintenance performed on each machine inside your plant can prevent these problems—minimizing shutdowns, expensive repairs, and other issues that can erode your bottom line and compromise your production. This blog will explain why recordkeeping is critical to your operation’s success and how you can use maintenance records to predict and improve future performance.
What is a maintenance record, and why is it important?
Equipment maintenance records are logs that systematically document all the work your team performs on the machinery in your processing plant. These records track details about equipment maintenance history, including service, inspections, repairs, and rebuilds.
The details logged in an operation’s maintenance records will vary from one processing plant to another. Most documents typically include information like:
- What type of service, repair, or other work was performed?
- When was the work assigned and completed?
- Who assigned and performed each task?
- How long did it take to complete?
- Which parts, materials, and other supplies were used?
- Were there other notes, observations, or photos from the technician?
Generally, the more accurate and up-to-date your equipment maintenance logs are, the more valuable information you can reap from these records.
What are the benefits of keeping equipment maintenance records?
Documenting each machine’s maintenance history lets you track its performance over time. These trends can be invaluable for deciding your maintenance schedule, equipment purchases, spare part inventory, and staffing.
Here are a few of the most significant benefits that recordkeeping can unlock for your processing plant:
- Finetune your preventative maintenance schedule.
Instead of waiting for equipment to break down (which will inevitably be more expensive to fix), use your maintenance records to proactively plan when a machine will likely need to be serviced or how often wearing parts need to be replaced. For example, if you know that the screens in your seed cleaning system need to be replaced more frequently than the manufacturer’s recommendations because of the seed type and quality you’re processing, changing out the screens can prevent rocks from sneaking through your cleaner, which could damage downstream equipment.
- Minimize unplanned downtime.
Unplanned downtime is the enemy of efficiency in a processing plant. Unless you have maintenance records to signal that a machine is approaching a major repair or rebuild, unexpected equipment failure could catch you unprepared, shuttering production until you can order a replacement. By contrast, your repair logs can help you predict and plan a maintenance turnaround when it fits into your production schedule and minimizes surprises.
- Optimize inventory management.
Thorough maintenance records help you prepare for upcoming repairs and rebuilds, including the necessary parts and tools. This allows you to forecast and control your inventory of spare parts and supplies with greater accuracy. For example, if your records indicate that your barrel liner needs to be replaced soon, and you don’t typically keep a backup, you can plan to order a new liner on time.
- Track capital expenditures.
By helping you predict the cost and timing of repairs, detailed records provide the forewarning you need to budget for maintenance expenses as part of your capital planning. Hiring specialized technicians to replace a barrel liner, for example, can be a hefty expense if it catches you off-guard. But when you use your maintenance records to schedule these repairs in advance, you can better plan your fiscal year and account for these costs, ensuring that profits keep flowing, along with oil production.
To uncover more benefits of keeping equipment maintenance records, download Anderson’s latest guide for the complete list.
Optimize your oilseed operation
Maintaining expellers, extruders, and other equipment is critical to any oilseed processing plant, and tracking these maintenance activities can drastically optimize your operation. With each maintenance cycle logged you gain more insights about your equipment to improve your workflow over time, making each maintenance turnaround more efficient than the last.
Contact Anderson International for help translating equipment maintenance records into operational improvements that boost your bottom line. With more than a century of experience building (and rebuilding) oilseed processing systems around the world, Anderson’s engineers and technicians can read between the lines of maintenance logs to maximize equipment performance and efficiency.