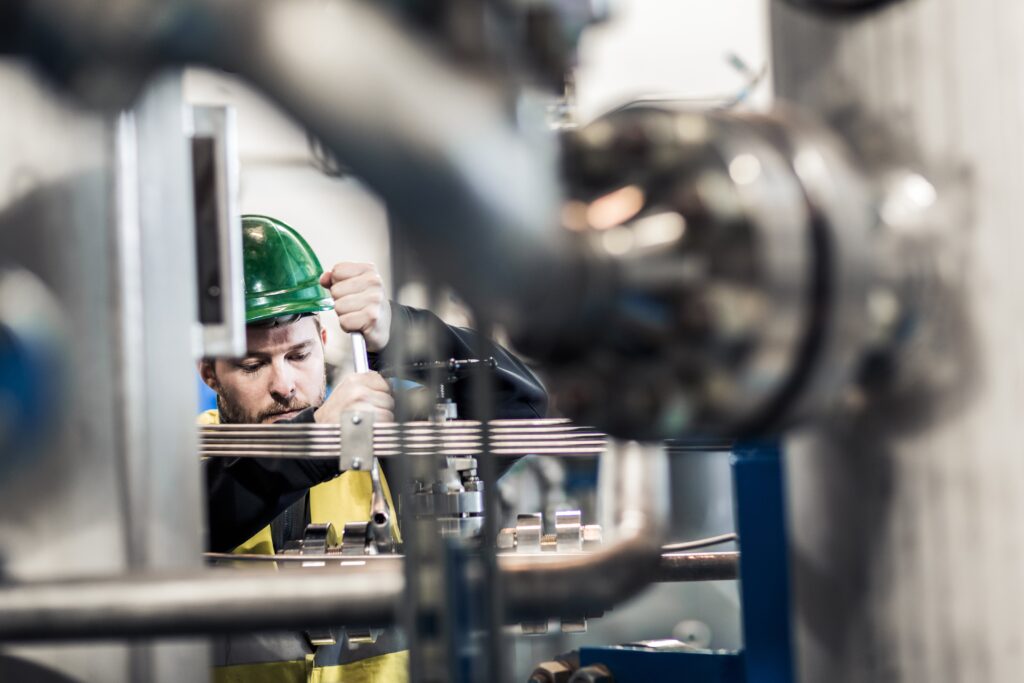
Oilseed expellers and extruders are composed of various parts that each play a critical role in the equipment’s overall operation. Inside each machine, major components like the shaft, barrel, and gearbox comprise several smaller pieces assembled. These screw press subassemblies can be complicated to repair and replace, often requiring the entire component to be removed from the machine and disassembled to fix a single part.
If your processing plant is shutting down production completely every time it breaks down, this laborious approach to maintenance could be tripling or even quadrupling your downtime—wasting precious hours that can impact your bottom line.
By stocking spare subassemblies and turning to Anderson International for rebuilds, oilseed processors can significantly streamline the maintenance burden of these components, unlocking several advantages to enhance production and profit.
What is a subassembly?
A subassembly refers to a group of parts that are put together to form a complete unit within a larger machine—in this case, a screw press. In other words, it is simply part of an overall construction, like building blocks that make up a bigger system.
The most common subassemblies inside oilseed expellers and extruders typically include:
- The barrel is composed of breaker bolts, knife bars, barrel liners, and frame components.
- The main shaft is made up of interrupted worm flighting along a rotating screw.
- The choke comprises moveable jaws, cone choke plugs, and extruder die plates in a discharge housing.
- The thrust unit consists of thrust bearings encased in lubrication oil.
- The gearbox may include the thrust unit in a single casing.
Instead of viewing equipment as one big, complicated assembly made of many individual parts, tackling maintenance in terms of subassemblies can make these complex systems more manageable.
The case for spare subassemblies
Let’s look at an example. During a routine inspection of the internal wearing parts of your screw press, you may notice that the worm flighting is showing signs of wear that are impacting your oil recovery rates. To replace the worms, you’ll have to remove the entire barrel, pull out the shaft assembly, remove the eroded worms from the shaft, replace them, and rebuild the unit before reinstalling.
Without the proper tooling for this job, some operators might use torches or hammers to force the worm from the shaft. Crude workarounds like this risk damaging parts or injuring employees. Plus, the time it takes to remove, repair, rebuild, and reinstall an entire subassembly—whether the shaft, the barrel, or the gearbox—can leave a plant offline far longer than necessary. When this downtime is unplanned, or part of a reactive response to an unexpected breakdown, it can be detrimental to production schedules and profits.
Now, imagine if you could remove the damaged subassembly and drop in a backup component from your inventory before you start rebuilding anything. Your processing plant could be back up and running again in a fraction of the time, and you can focus on rebuilding subassemblies without holding up production.
Also read: Troubleshooting Common Expeller Press Malfunctions
The tools and expertise for rebuilding
Even with spare subassemblies on hand, rebuilding screw press components requires a high level of mechanical expertise, not to mention the right tools for the job—which, in this case, should be a bit more sophisticated than torches, hammers, and brute strength.
To further streamline the technical complexities of rebuilding these components, simply send damaged parts to Anderson and let our experienced service technicians handle the work. We’ll send back the rebuilt component as good as new, so you’ll have it ready and waiting for the next rotation.
Whether you send us your damaged subassembly or have our technicians take it out themselves, we will bring the component back to our warehouse, where we have the right tooling and expertise to disassemble and rebuild parts to OEM specs properly. Using our large hydraulic press, for example, we can push the eroded worms off the shaft assembly much more quickly, safely, and cost-effectively—significantly minimizing the risk of damaging parts or injuring workers.
Anderson has over a hundred years of expertise in rebuilding these components to keep oilseed processing equipment running at peak performance. Leveraging our expertise for these complicated rebuilds can reduce the technical knowledge required of your in-house mechanical team to maintain these components so you can focus on crushing seeds.
The benefits of subassemblies
The example above highlights many of the advantages that operators can unlock by partnering with Anderson to supply and rebuild their screw press subassemblies. These benefits include:
- Minimizing downtime: Swapping out a worn or damaged subassembly with a spare component can minimize unplanned downtime, bringing production back online faster.
- Reducing costs: Unplanned downtime can be expensive in terms of lost profits and interrupted production. Minimizing disruptions can significantly reduce these costs.
- Leveraging technical expertise: Relying on Anderson’s service technicians to rebuild your components can alleviate the burden of building this mechanical expertise in-house.
- Accessing proper tools: Similarly, having Anderson rebuild your screw press subassemblies saves you from investing in the tools required to safely tear apart these components.
- Maintaining quality: Compared to improvised in-house fixes, Anderson’s equipment rebuild services maintain the OEM specs’ precise tolerances and quality standards.
By proactively planning for subassembly rebuilds, stocking spare components, and turning to Anderson’s technical service expertise, processors can maximize the value of their screw press subassemblies to keep plants running without a hitch.
Take control of your subassembly components by contacting Anderson’s service technicians today.