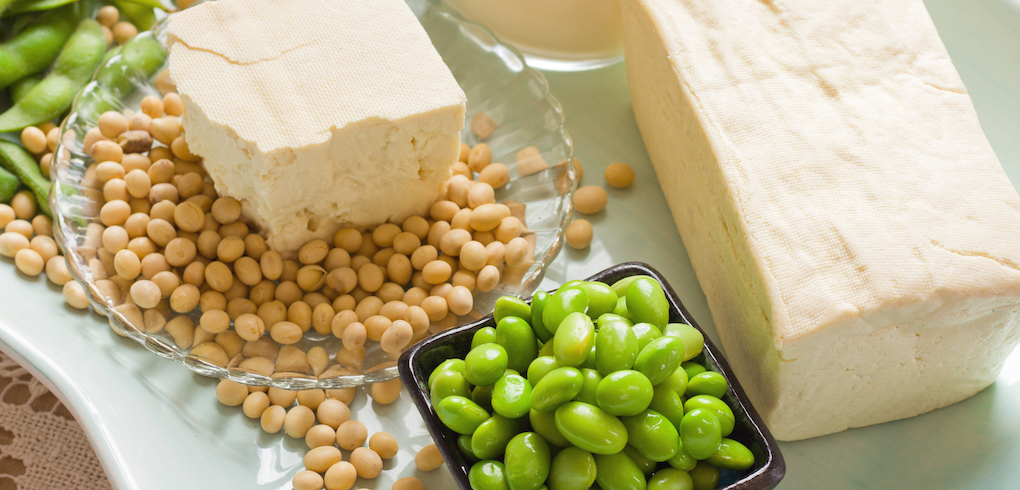
Good news for oilseed processors: the plant protein market is heading towards an all-time high. A new research study by The Insight Partners projects that plant protein is expected to grow at a CAGR of 6.2% from 2019-2027 to reach a value of 28 million USD by 2027.
Processors have the potential for high profits as the market expands, but these gains are dependent on meeting specific conditions of the growing consumer demand. Let’s look at the driving factors behind plant protein growth, oilseed processing system design, and how extrusion technology enhances soy processing.
Why plant proteins
Protein is a macronutrient that is essential for good health. It is a critical part of processes in the body that impact energy, transport oxygen, and create new cells and antibodies that fight infections and illnesses. A building block of your body, it is found in everything from organs, muscle, and tissue to your bones, skin, and hair.
But not all protein is created equal. Compared to animal protein, plant protein is a healthy alternative that can lower the risk of several diseases. Plant proteins also emit fewer greenhouse gasses and are more sustainable than animal proteins. When combined with the lower cost of producing plant proteins, these factors drive the trend towards more meat alternatives in the food manufacturing industry.
Currently, the plant protein market is dominated by soy, wheat, and pea. Of the three, soy holds the largest share. Soy is an exceptionally low-cost source of protein, providing essential amino acids for nutrition. It can help reduce cholesterol levels, decrease cancer risk, and increase metabolism and bone mineral density.
Of course, soy is not a new product in the oilseed industry. What is new, however, is the growing emphasis on nutrition and the environment. Not all established processing methods pair with these latest consumer demands.
One method of processing – high-shear extrusion – stands out for its ability to meet the needs of health and environment-conscious consumers.
Extrusion technology enhances soy processing
Extruders are an ideal option for processors that want to set themselves apart in this growing market. An extruder, like the Anderson Dox™, works ahead of a press to shear, dry, and cook the oilseed. The Dox uses high heat combined with a short residence time to deactivate harmful enzymes, flash-dry excess moisture, and cook the protein for efficient pressing.
This technology provides several significant benefits:
Nutrition
Soy is well-known for its nutritional value; however, components present in raw soybean negatively impact its overall quality. Anti-nutritional factors, such as urease and trypsin inhibitors, impair protein digestion and valuable nutrients when consumed.
For customers to benefit from the plant’s protein, manufacturers must destroy anti-nutritional factors using adequate heat during processing. However, too much heat will degrade the protein and risk nutrition. Processors must apply enough heat, but not too much, to destroy the anti-nutritional factors adequately while also strengthening the protein.
Dox extrusion technology uses high heat, with a short residence time of about 30 seconds, to provide optimal conditions for destroying harmful factors while maintaining the quality of the protein. This high-heat application also helps limit oxidation in the expelled oil, another added benefit for processors.
An additional health benefit is that an extruder and press system does not use harmful chemicals during processing. Solvent extraction is most widely accomplished with hexane to separate the solids from the fats during processing. However, hexane is labeled a carcinogen and can have a detrimental impact on human and animal health.
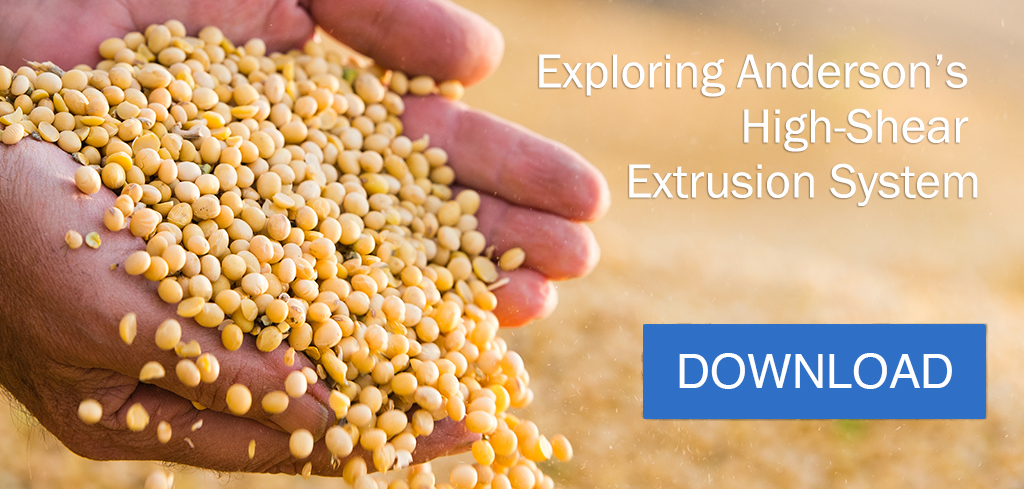
Read more: Soybean Meal: Protein Solubility vs. Protein Dispersibility Index
Environment
In addition to being harmful to human health, hexane has been identified by the U.S. Environmental Protection Agency as a widely occurring atmospheric pollutant. Research published in recent reports shows that oilseed processing plant use of hexane during solvent extraction releases significantly more hexane into the environment than other food manufacturing sectors.
The extruder system resolves this environmental challenge by eliminating chemicals during processing. Instead, high-shear extrusion technology uses mechanical energy to generate the heat needed for cooking. The screw press uses pressure to compress the seed to separate the fats from the solids.
Another environmental benefit is that the Dox can reduce the energy consumption of processing plants. Mechanical force in an extruder creates the heat necessary to prepare the oilseed for the press without an external heat element or steam. This design eliminates the need for boilers and replaces energy-consuming machines like flaking mills, dryers, and cookers.
In addition to reducing machinery, the extruder and press system requires a smaller footprint, and in terms of energy, requires a lower cost per ton than a traditional processing plant.
The Dox is also known for doubling the life of pressing equipment parts. As a result, spare parts are needed less frequently, reducing processing plant waste. As a bonus to manufacturers, costly downtime is decreased significantly since high-wear parts last longer before replacement is necessary.
Read more: How high-shear dry extrusion advances greener oil milling
As the trend towards plant proteins grows, processors should consider investing in machinery that will meet market demands. An investment in extrusion technology will not only preserve the nutritional value of soybeans and reduce negative environmental impact, but processors benefit by increasing efficiency and reducing downtime in their facility. These benefits will allow processors to garner increased profits from the projected growth of plant protein demand over the next several years and beyond.
For a same-day quote on Anderson’s high-shear dry extrusion system, contact us here.