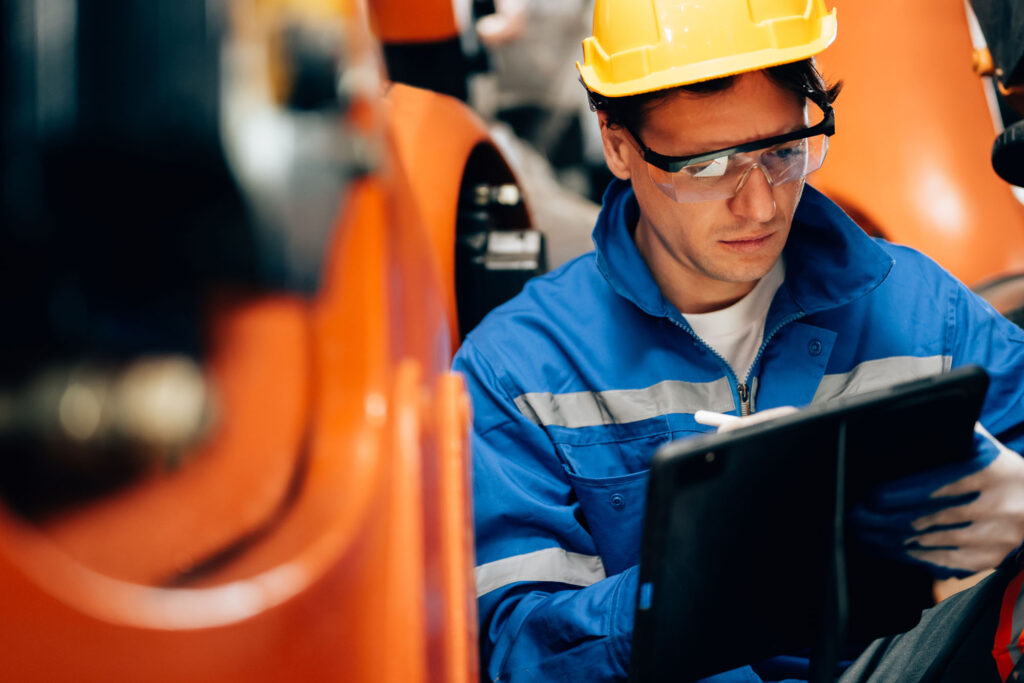
Process efficiency and product quality are the twin peaks of excellence in any production facility. In oilseed processing plants, the goal is twofold—to extract as much quality oil as possible while consuming as little energy as possible. However, when production managers get tied up running day-to-day operations, they can’t always see the forest for the trees—or the soybean fields for the individual seeds. By conducting a comprehensive oil mill process audit, operators can bring in a fresh set of eyes to objectively assess every aspect of production that might get overlooked in the daily grind.
Processing audits can reveal inefficiencies and bottlenecks that may impede the flow of quality products and profits, while pinpointing opportunities for improvement. A critical catalyst for quality and efficiency, process audits can keep plants on track to meet production goals and product specifications, uncovering huge potential savings along the way.
This blog will explain what’s involved in a mechanical extraction plant audit and how a quick “oil mill health check” can optimize your operations.
What is an oil mill process audit?
Known in some industries as a manufacturing audit, a quality assurance audit, or simply a production process audit, this describes a systematic assessment of a plant’s overall production processes, systems, and outputs. An oil mill process audit includes careful observation of a mechanical extraction plant’s workflow, a thorough evaluation of every piece of equipment involved, and a close quality inspection of the oil and meal byproducts produced.
A thorough oilseed processing assessment might consider each machine’s performance, capacity, energy efficiency, and the overall sequence of operations as material moves through the plant.
Oil mill process audit checklist
A comprehensive process audit should analyze the entire extraction process from start to finish—starting with the storage of incoming raw seed material and concluding with the finished oil and meal byproducts. In between those two points, a range of complex steps impact the efficiency of the overall process, from preparation to extraction to product handling.
While the exact steps and sequence of operations may vary between plants, depending on the types of seeds processed and the end-markets served, the steps assessed in an audit generally include:
- Seed storage – Silos and storage tanks protect raw seed material from mold, bacteria growth, and pest damage by maintaining ideal conditions in terms of temperature and moisture level.
- Seed cleaning – Vibrating screens, magnets, aspirators, and destoners remove leaves, sticks, stones, and other foreign material from the oilseed. Removing this debris increases the meal’s protein content and improves oil yields while protecting downstream equipment from abrasive non-seed material. Seed cleaning even helps reduce operating costs by ensuring no energy is wasted on transporting, heating, or crushing foreign material.
- Side reduction – Roller mills, grinders, hammer mills, and flaking and cracking machines break tough oilseeds into smaller pieces to promote more efficient oil recovery. However, using the right tool for the job is critical. For example, using a hammer mill instead of a cracking roll could grind certain seeds too much, creating particles too fine for the downstream press to process efficiently.
- Heat treatment – High-shear extruders, roasters, dryers, seed conditioners, and other machines generate heat throughout the extraction process via steam heat or mechanical friction. Heat treatment is an important step to rupture the oil-bearing cells of the seeds while also deactivating harmful enzymes and anti-nutritional factors. However, excessive heat exposure can scorch the oilseeds, degrading the quality of the resulting byproducts. Just a few degrees and several minutes’ variance in drying time can make a big difference in oil recovery and product quality.
- Oil recovery – Oil expellers and extruders physically crush seeds to separate valuable liquid oil from solid seed meal. With many moving parts involved in the mechanical extraction process, each individual part of these machines can impact the operation’s overall efficiency. Regular maintenance and proper equipment operation also play significant roles.
- Oil clarification – Decanters, centrifuges, filters, and settling tanks remove solid impurities from the expelled oil to ensure the highest quality product with the highest possible market value.
- Meal handling – Defatted cake is cooled and ground into meal after extraction. The protein content and composition must meet quality assurance standards before the meal hits the market.
During an oil mill process audit, the process engineer will measure the performance, capacity, and energy footprint of every machine involved in each step described above. This consists of documenting how much horsepower is connected to and used by each piece of equipment. For example, if a screw press with 300 connected horsepower is rated to process six tons of product per hour but it’s only crushing four tons per hour, the audit will flag the press for further inspection. Likewise, if a seed cleaner is only sized for 10 tons per hour but is pushing 15 tons, it won’t perform at peak—and could add unnecessary costs and risks.
In addition to evaluating the process step-by-step, a thorough extraction plant audit will also measure the quality of the end-products produced. Samples are collected of raw materials, clean seeds, conditioned seeds, expelled product, clarified oil, and cooled meal and sent to a third-party laboratory to objectively measure quality throughout the production process. Extraction may seem efficient based on observation alone, but if, for example, the lab tests indicate excessive trypsin inhibitor activity in soybean meal, then the audit will reveal this quality issue.
The value of Anderson’s processing audits
Over the last 130 years, the process engineers at Anderson International have designed, manufactured, commissioned, and inspected processing systems at more than 1,000 plants processing more than 100 different materials in more than 100 countries. We’ve seen it all, so we know exactly what to look for when evaluating and optimizing oil mill operations. Anderson’s deep knowledge of the nuances involved in oilseed processing is an indispensable resource for operators trying to enhance quality and improve efficiency.
Our experienced applications engineers who perform plant audits specialize in oil mill efficiency. They analyze every detail of a processing system to pinpoint potential issues and recommend—and even design, install, and implement—the appropriate solutions. Whether a simple mechanical fix or a more strategic process improvement, our audits include detailed recommendations to streamline operational inefficiencies and optimize oil recovery.
Anderson’s goal when conducting an oil mill process audit is the same as yours: to extract as much oil as possible, using as little energy as possible, while maintaining product quality. That’s why our audit recommendations always prioritize the lowest-hanging fruit. We tailor our solutions to attack the lowest-cost fixes with the highest payback to impact your operations positively. We’ll never recommend a hefty investment in a new machine, for example, if we can just replace a single wearing part or adjust a small setting that could save energy.
By scheduling a processing audit at least once every five to 10 years, oil mills can unlock value by:
- Identifying inefficiencies to enhance production processes.
- Minimizing unnecessary energy costs.
- Improving oil yields by optimizing the extraction process.
- Ensuring production goals and product specifications are met consistently.
- Mitigating potential processing issues before they escalate into problems.
- Gaining valuable operational insights to make better decisions.
- Maintaining top-quality oil and meal production.
After all, we aim to help our clients maintain more sustainable, efficient oilseed processing operations. A comprehensive oil mill process audit can be a powerful tool to achieve that goal.
To schedule a processing audit of your mechanical extraction plant, contact Anderson’s applications engineer today.