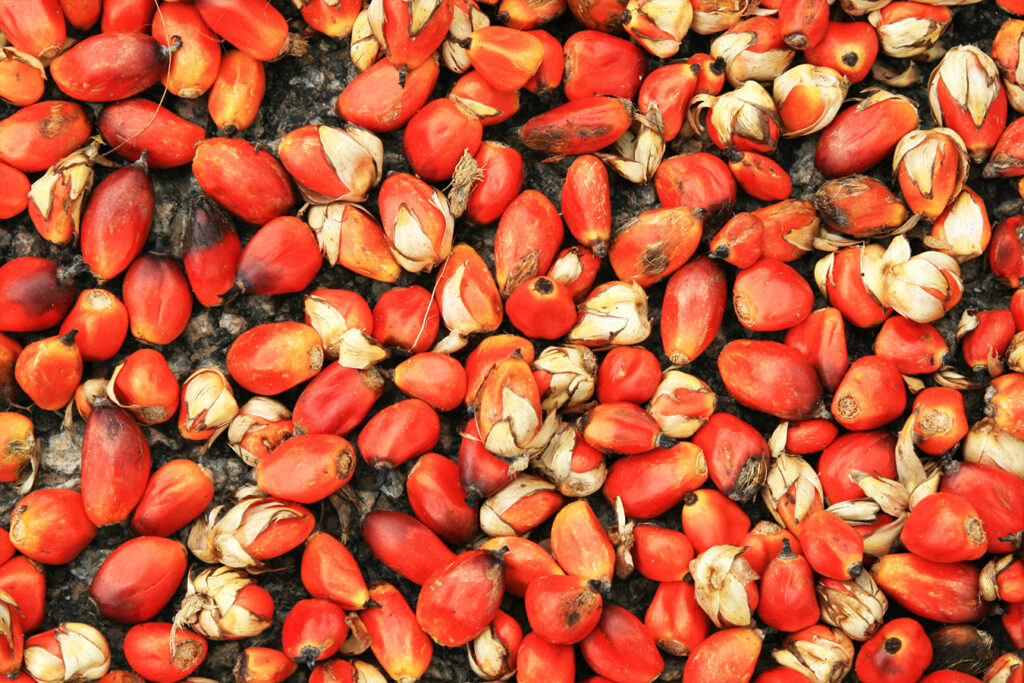
In the oilseed processing industry, every type of nut, seed, and bean comes with unique processing considerations and opportunities. Each seed requires special treatment to efficiently produce high-quality oil and nutritious meal, from cleaning and cracking to cooking and drying to crushing.
So, before MIDIKA International could start offering toll processing services to help its customers crush a wide range of oilseeds for various end-markets, the company needed a mechanical crushing plant that would be versatile enough to press any seed. An industrial equipment distributor and Anderson’s exclusive distributor in Mexico, MIDIKA, partnered with Anderson to build a pilot plant with the flexibility to pivot between materials and markets.
Here’s a closer look at how MIDIKA’s toll crushing plant came together.
The opportunity for toll processing services
Between all the industrial equipment, specialized expertise, and intricate steps required to run a crushing facility, oilseed processing can be a massive undertaking. To tap into these capabilities quickly with lower costs and reduced risks, companies may outsource their crushing operation to a toll processing partner like MIDIKA to explore new markets, test new products, or ramp up production.
Since different types of oilseeds require different processing steps and systems, toll processors must be set up to handle a wide range of seed types and pressing methods. For example, some of MIDIKA’s customers want to use traditional expeller-pressing methods that utilize heat, otherwise known as “hot pressing.” In contrast, other customers require their seeds to be cold-pressed with minimal heat exposure to preserve crucial nutrients. Offering both types of pressing methods was critical to MIDIKA’s operation—but this also presented challenges.
- Traditional pressing methods utilize heat for cooking and drying seeds, allowing for more efficient oil recovery in the press. Heat treatment is an essential step in breaking down the cellular structure of the seeds, releasing oil so it flows more freely. The press’s friction and mechanical force generate additional heat exceeding 200 degrees Fahrenheit. This traditional hot pressing method can remove about 80-90% of the oil from the seeds.
- Cold pressing, on the other hand, aims to extract oil without adding heat. This process eliminates the upstream heat treatment involved in cooking and drying the seeds, instead sending raw materials straight to the press. Since this “cold” material hasn’t been cooked or dried to release the oil from the seeds, the screw press has to work even harder to extract the oil using force alone. Therefore, cold pressing requires more torque to squeeze the oilseeds longer and harder. Some processors achieve this by running multiple presses or running the material through the same press two or three times, but this duplication adds extra time, energy, and overhead costs. Plus, the extra mechanical force generates even more frictional heat inside the press, requiring additional cooling controls throughout the process.
To offer the most flexible toll processing services, MIDIKA’s challenge was utilizing the right equipment to efficiently crush a variety of seeds, with or without added heat, while achieving residual oil levels between 6-8 percent.
Download our case study about MIDIKA’s mechanical toll crushing plant.
The solution: Anderson Super Duo and Dox
The Anderson Oilseed Division Team of Sales, Project Management and Engineering worked closely with MIDIKA and their general contractor to design a flexible mechanical crushing plant to accommodate the company’s toll processing services. Understanding that MIDIKA’s crushing process will vary depending on the product being pressed and the customer’s unique specifications, Anderson turned to two of its most versatile oilseed processing machines: The Super Duo 600 Expeller press and the Dox 450 Extruder.
- The Anderson Super Duo™ Series Expeller® gives MIDIKA the greatest flexibility for toll processing services because it can crush many different types of seeds and nuts, including difficult-to-process specialty materials like copra, palm kernel, and cottonseed. Due to the difficulty of extracting oil from these tough materials—especially when cold-pressing them without added heat—many processors run these products through the press twice to recover more oil.
The Super Duo 600 offers a more efficient solution with its unique dual press design—providing the highest torque per ton of product processed, which is critical in cold pressing. This design incorporates both a horizontal and a vertical expeller press in one machine, allowing the lowest possible residual oil levels in a single pass. Additionally, the Super Duo features built-in barrel cooling and flushing systems, along with optional water cooling on the horizontal shaft, for the most precise temperature control when cold pressing.
- The Anderon Dox™ Extruder expands the versatility and efficiency of MIDIKA’s toll processing services by adding heat to optimize the process. Ideal for materials like soybean, canola, and sunflower seed, this multifunctional machine mechanically cooks, dries, and shears oilseeds to prepare material for optimal pressing. The high-shear environment ruptures the oil-bearing cells within the seed and generates frictional heat—which deactivates harmful enzymes, flash-dries excess moisture, and quickly cooks the proteins.
Installing a Dox upstream of an Expeller doubles the capacity of the press and the life of the pressing parts while reducing energy usage to make MIDIKA even more efficient. In addition to improved oil recovery, the high-shear extrusion system helps improve the nutritional value of the meal byproduct, as well—enabling MIDIKA to produce Anderson’s chemical-free, sustainably-produced ECOMEAL™ and a range of other products.
While the new toll crushing facility was being commissioned, the Anderson Oilseed Division Team and its Anderson Vendor Partners provided hands-on training to MIDIKA’s team to ensure a smooth hand-off as the plant prepared to open.
The results at MIDIKA
Anderson worked with MIDIKA over the course of a year to turn a greenfield site in Salamanca, Guanajuato, Mexico into a functioning mechanical crushing plant capable of processing various products. Running a Super Duo 600 expeller press and a Dox 450 extruder, the pilot plant can process up to one ton of product per hour, while easily pivoting between different raw materials or from hot to cold pressing methods. Depending on the material and customer specifications, these machines achieve residual oil levels between 6-8 percent.
By leveraging industry-leading equipment from Anderson International along with proven best practices in specialty oilseed handling, extrusion, and pressing, MIDIKA is positioned to meet a wide range of customer requirements. Anderson’s high-shear extrusion system, comprising the Super Duo expeller paired with the Dox extruder, helps MIDIKA achieve best-in-class oil recovery while lowering energy usage. This equates to the lowest total cost of ownership, as measured by uptime tonnage produced and energy consumed—enabling MIDIKA to offer a range of toll processing services for commercial use, as well as research and development.
With this toll crushing plant now fully operational, MIDIKA and Anderson will continue to partner to offer training, research and development, and mechanical toll processing services to our oilseed customers in Mexico and the U.S. Contact us to learn more about the mechanical crushing capabilities of Anderson’s oilseed processing equipment.