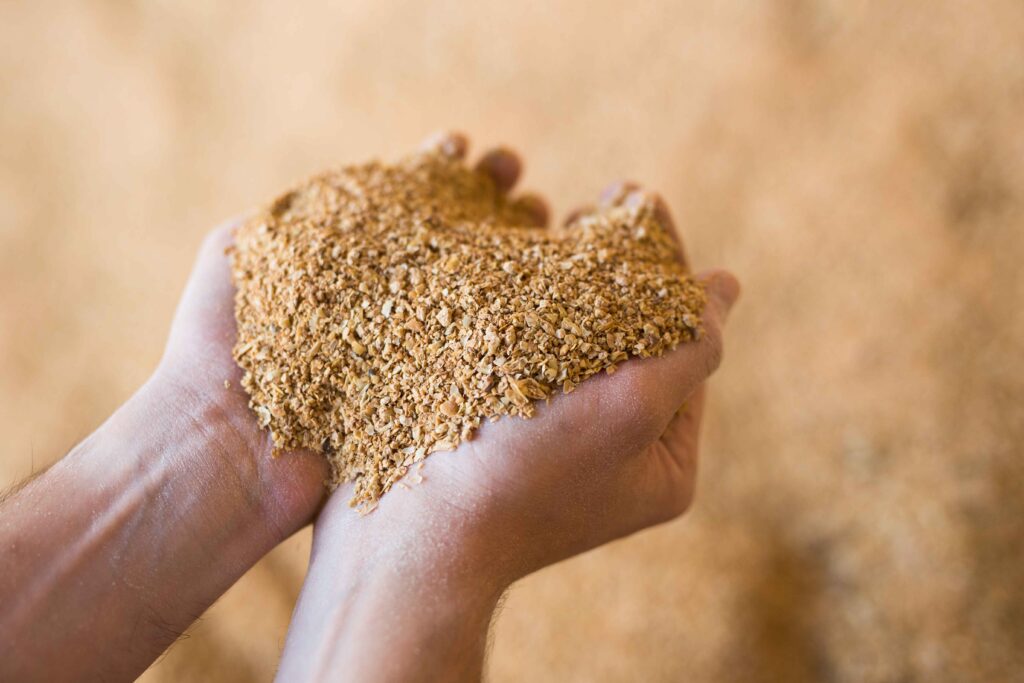
Extrusion technology has been used to process grains and seeds for nearly a century. As processing methods evolved, extrusion systems like Anderson’s popular Dox™ Extruder have advanced to become essential apparatus in many operations. But long before the Dox was invented, Anderson’s feed extrusion expertise originated with a modest machine called the Expander-Extruder-Cooker™, or EEC.
As the predecessor to Anderson’s modern extruders and expanders, the EEC set a new grain and oilseed processing standard. In fact, hundreds of EECs are still in operation worldwide today—producing highly nutritious and economical meals for pets, pigs, poultry, fish, livestock, and even human food. By blending the best aspects of extruders and expanders into one heavy-duty processing powerhouse, the EEC’s simple design and durable engineering have endured for almost a century.
In this blog, we’ll explain what makes the EEC so valuable and versatile for feed extrusion as we explore the benefits of extruded animal feed.
The accidental invention of the EEC
As the story goes, an oil mill operator unintentionally invented a new processing technology one day when he forgot to set spacers between the bars inside the barrel of Anderson’s screw press expeller. This accidental modification sealed the chamber to make a solid barrel cage, inadvertently creating a continuous pressure cooker that transformed the material inside.
When the operators ran dry processed corn germ through this pressure cooker, they noticed the corn popping and puffing up as it exited the expeller. The end product’s ‘expanding’ nature provided a name for the new technology: Anderson’s Expander-Extruder-Cooker™. Eventually, Anderson’s engineers adapted the basic design of the EEC to spawn both the Solvex Expander and the Dox™ Extruder.
But what caused this game-changing expansion, and why was it so beneficial for feed production? By analyzing the science behind this accidental invention, Anderson enhanced the feed extrusion process to revolutionize processing with the EEC.
The feed extrusion process
Dry grain or seed material like corn germ or rice bran is conveyed through the EEC and mixed with steam and water injected directly into the barrel. The EEC’s proprietary interrupted worm flight design thoroughly blends the material into a homogenous mass, and the shearing action of the rotating worms breaks apart the cell walls to make nutrients more accessible.
Frictional heat from the rotation of the screws inside the barrel, combined with thermal heat supplied by steam injection, accelerates heat transfer inside the EEC. The heat and pressure generated inside the sealed barrel create a continuous pressurized cooking vessel, like the pressure cookers found in many kitchens. These conditions rapidly cook grains and oilseeds in seconds using the High Temperature – Short Time™ (HTST) principle. Faster cooking times increase machine capacity while reducing energy consumption—making the EEC super-efficient.
The combination of heat, pressure, moisture, and mastication inside the EEC triggers several crucial reactions that transform the raw material. Perhaps the most critical reaction that happens during feed extrusion is starch gelatinization. Starch granules, which are naturally too densely compacted to absorb water, swell under the conditions of the EEC until they burst and become soluble and adhere into a sticky, gelatinous glob. When this gel is discharged from the machine, the sudden drop in atmospheric pressure forces the injected moisture to instantly vaporize—leaving a network of tiny pores that causes the material to expand.
This extruded material is discharged from the EEC through die plates with various openings that produce a range of different shapes. The die restricts the product flow exiting the machine, building up the pressure needed to create expansion. Then, a cutting knife assembly slices the extruded product into the desired length. By modifying the die plates and cutter assemblies, operators can produce a variety of extruded product sizes, shapes, and textures.
The benefits of feed extrusion
Starches aren’t the only compounds that transform during feed extrusion. The high-pressure, high-temperature environment inside the EEC also denatures proteins, unlocking several additional nutritional benefits in extruded feed materials:
- Deactivates enzymes. The pressure cooker environment inside the EEC effectively stabilizes harmful enzymes and anti-nutritional factors that can interfere with nutrient absorption, such as urease in soybeans and lipase in rice bran.
- Destroys bacteria. The high temperatures in the EEC also kill bacteria, mold, and unwanted microorganisms to improve the hygienic quality of extruded feed.
- Improves digestibility. The simultaneous gelatinization of starches and denaturization of proteins makes extruded feed easier for animals to digest. Dogs, for example, cannot digest raw starch, so the feed extrusion process provides this essential energy source in an easily digestible form.
- Improves nutrient availability. Although the feed extrusion process produces enough heat to destroy harmful enzymes and bacteria, the short residence time of the EEC prevents material from overcooking—preserving heat-sensitive amino acids in the proteins. Extrusion improves the bioavailability of these and other essential nutrients, enhancing nutrient absorption to improve the feed utilization rate.
- Improves palatability. The extrusion process develops crisp textures and desirable flavors that make the feed more palatable for many animals, such as cats, dogs, poultry, pigs, and horses. This can encourage improved feed intake, leading to improved nutrition and performance.
A valuable tool in animal nutrition, extrusion offers numerous benefits that contribute to the production of high-quality, highly digestible, and nutritious animal feeds.
Extrusion applications
Whether grain and oilseed materials require a simple cooking application or more robust processing of complex formulated and shaped products, Anderson’s EEC 800 offers the flexibility to manufacture a wide range of extruded ingredients.
Some of the most common applications for the EEC 800 include:
- Full-fat soybean meal
- Gelatinized corn starch
- Textured vegetable protein
- Dry pet food for cats and dogs
- Floating and sinking aqua feed
- Animal feed for poultry and livestock
For operators looking to break into these markets, the EEC makes an excellent starter machine that is both highly efficient and incredibly cost-effective. The magic of this machine is its rugged simplicity. Most notably, the EEC:
- Doesn’t cost a lot to operate, offering a lower capital investment at roughly one-third to one-quarter the price of competing extruders and expanders.
- Doesn’t require pre-treatment vessels to condition material before extrusion because it thoroughly cooks and rapidly blends products with its high-shear mixing action.
- Doesn’t require frequent or expensive maintenance since its wearing parts can process between 10,000 to 30,000 tons of feed material between overhauls.
Engineered to withstand extreme processing conditions and difficult-to-process seeds, the EEC is built to last. Its rugged construction and efficient design bring a world of benefits to the feed extrusion process, enhancing the nutritional quality and digestibility of valuable ingredients while unlocking numerous processing advantages—and profits—for operators.
Contact us today to discover how Anderson’s EEC can expand your plant’s market and profit potential.