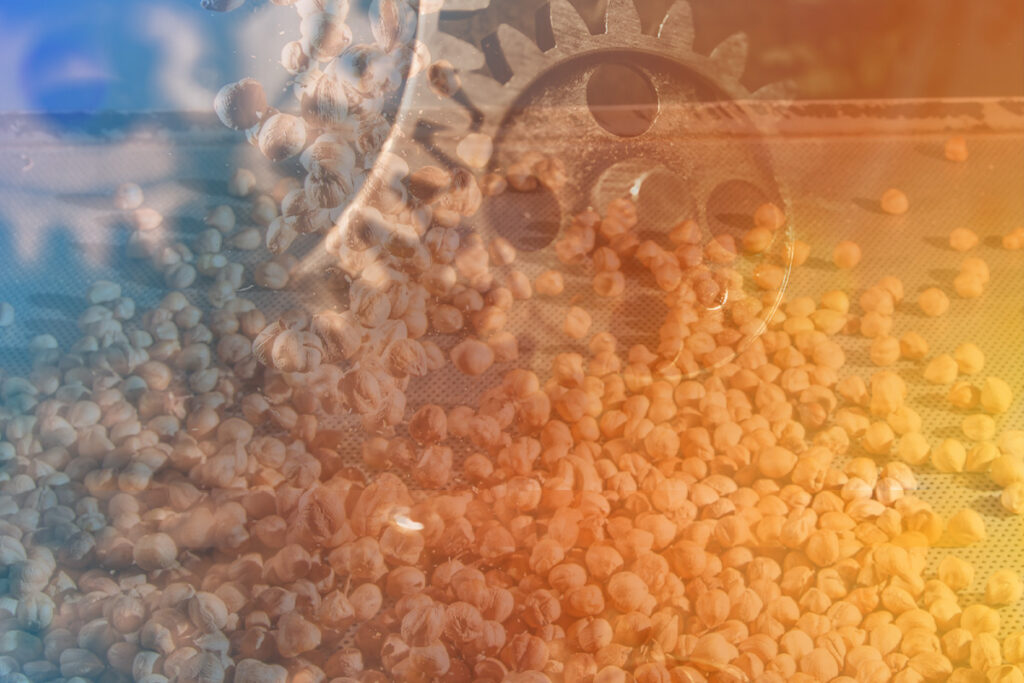
Inside a mechanical oil press, the main worm shaft is known to compress seed material to squeeze out valuable oil while the motor powers the press. A critical component connects these two crucial machines: the gearbox.
This blog will answer some of the most frequently asked questions about screw press gearboxes to explain their importance in oilseed processing plants.
Let’s take a closer look at the vital component that keeps screw presses running.
What is a gearbox?
A gearbox is a common mechanical component that transfers energy or force from the power source (like a motor) to the rest of the system (in this case, a screw press). In a mechanical press, they connect the motor to the main worm shaft, converting electrical energy from the motor into mechanical energy that rotates the shaft to keep seed material moving through the barrel.
The component contains gears and bearings encased in oil to lubricate the individual parts and minimize the friction of the gears grinding against each other, allowing them to rotate freely.
What does a gearbox do?
The primary functions of gearboxes are to transfer motion and increase torque. In other words, it amplifies the mechanical force of the motor to rotate the worm shaft inside the screw press, which requires substantial torque.
Any electric motor runs at a certain speed to produce a certain amount of torque. But to meet the requirements of the machine it’s powering—that is, to spin the shaft at the right speed to efficiently crush the oilseeds in the screw press—demands a different rotational speed and torque than the motor provides directly. That’s where the gearbox comes in.
Read more: Inventing the First Continuous Mechanical Screw Press
What size gearbox do I need?
Gearboxes must be sized appropriately to suit each application in a screw press based on the speed and torque produced by the motor (input) compared to the speed and torque needed to turn the worm shaft (output).
This difference is measured by the “reduction ratio,” or “gear ratio,” which measures the difference between the input and output speeds of the gears. The pinion shaft from the motor is connected to a smaller gear, which spins much faster than the larger gear it turns, which is connected to the worm shaft. The difference between the sizes of these gears—the reduction ratio—determines how much it must reduce the rotor speed from the motor before it gets to the shaft. This same ratio that reduces the output speed also multiplies the output torque.
For example, if the diameters of a small pinion gear and a larger corresponding gear differ by a ratio of 60:1, that gearbox on an 1800 rpm motor would produce a 30 rpm output speed for the main worm shaft. While reducing the rotational speed by the amount of the reduction ratio, the component also multiplies the torque by the same amount—transferring the power required to compress the seeds.
How long do gearboxes last?
The value of a gearbox is determined by how much torque it can handle and for how long. When selecting gearboxes to power oilseed processing plants, operators should consider the torque rating and the rated lifetime of gears and bearings. The more torque it can handle and the longer the expected wear life of its parts, the higher its value.
However, the lifespan of gears and bearings can vary widely depending on how well they’re maintained. While mechanical components from Anderson International come with a one-year warranty, many of our clients keep their gearboxes running for five to 10 years before requiring major repairs or replacements. As with all mechanical processing equipment, the better you take care of it, the longer it can be expected to last. Speaking of which…
How much maintenance do gearboxes need?
Gearboxes play a significant role in mechanical crushing operations, and as such, they are subject to considerable wear and tear. While the lubrication oil helps protect the gears and bearings from metal-on-metal contact, these parts will naturally degrade over time. Preventative maintenance is essential to maintain peak performance while minimizing costly repairs and unplanned downtime.
Recommended maintenance procedures include:
- Check lubricating oil levels daily and refill to recommended levels if necessary.
- Analyze oil quality monthly to look for metal shavings, solid particles, or other contaminants that might indicate unusual gear wear or bearing failure.
- Monitor equipment during operation and make note of any unusual noises or vibrations that may indicate mechanical problems.
- Change lubricating oil and replace oil filters at least once every 8,000 operating hours.
- Inspect all oil seals around the input and output shafts for leaks or damage at least quarterly, if not more often.
- Monitor the temperature of the lubricating oil continuously, as excessive friction from metal-on-metal grinding could cause it to overheat. A cooling system can help control oil temperatures.
For more maintenance tips, download Anderson’s guides to expeller maintenance and extruder maintenance.
Where can I get gearbox service and support?
Anderson International has more than a century of experience designing, installing, and maintaining oilseed processing systems around the world, so our gearbox expertise runs deep. Anderson’s technical service team offers rebuild services for screw press gearboxes, and our rebuilt units come with the same one-year warranty as new products.
In addition to rebuilding, repairing, and replacing parts, Anderson’s service technicians also provide technical expertise to help processors troubleshoot, provide operational training, and fine-tune their maintenance procedures. Beyond mechanical maintenance, Anderson’s application engineer offers another level of support by analyzing plants via process audits and designing effective solutions to optimize an overall operation—ensuring efficiency from the gearbox all the way to the oil tank.
Have more questions about your screw press and its mechanical components? Contact Anderson today.