Anderson’s line of Expander-Dryers has proven to be the most cost-effective way to finish drying synthetic rubbers.
Anderson’s Expander/Dryer was invented and the process patented by Anderson to provide processors with a new technology for mechanically drying fresh crumb rubber (synthetic or natural) with moistures of 6 to 15% down to ≤ 2%. The Expander/Dryer is the heart of Anderson’s process patent for the “Total Mechanical Drying of Synthetic Rubber.” All present‐day mechanical finishing technology is roughly based on Anderson’s patent.
The process patent is based on the thermodynamics properties of “Enthalpy” and “Entropy.” The Expander is designed to develop the necessary internal process conditions involving pressure and temperature while the Expeller is used to regulate the fluid (water) in the system. When operated properly, up to 90% of the moisture contained in the rubber will “flash‐off” as steam at the die plate, immediately cooling the crumb rubber and producing a porous crumb ideally suited for low energy cost downstream hot‐air finish drying.
Highlights
- Most widely used and economically feasible means of separating process moisture from crumb rubber
- Obsoleted the use of “thermal Dryers” for finishing a wide range of commodity elastomers
- Expander models designed for capacities (dry base) from 100kg/hr. to 12,000kg/hr
- Anderson Mechanical Drying Technology is used worldwide is most solution-based polybutadiene and styrene‐butadiene rubber production facilities
- High‐efficiency conversion of torque to energy in the process will produce the highest degree of “Evaporative Cooling” at the Expander die plate
- Anderson’s staff of process experts can offer unparalleled processing support to users based on hundreds of operating installations
Features
- Anderson manufactured reducer/thrust cases
- Standard 316 stainless steel materials in the process flow with availability of high‐alloy materials for corrosive processes
- Connected power from 50 HP (37.3kW) to 2,400 HP (1789kW)
- Remote control of the process with Anderson’s PLC control panel
- Barrel liners full length are replaceable, providing long‐life of barrel sections
Applications
- All types of synthetic crumb rubber, natural rubber, reclaim rubber, block copolymers and most all non‐vulcanized elastomers
- Used to produce crumb rubber that is suitable for finish drying in downstream mechanical drying extruders or hot‐air dryers
- Will not change the molecular properties of the polymer
- Produces semi‐porous pellets for SIS, SBS, SEBS, TPE’s, HSR, etc.
Shown here: Anderson 14A Expander-Dryer
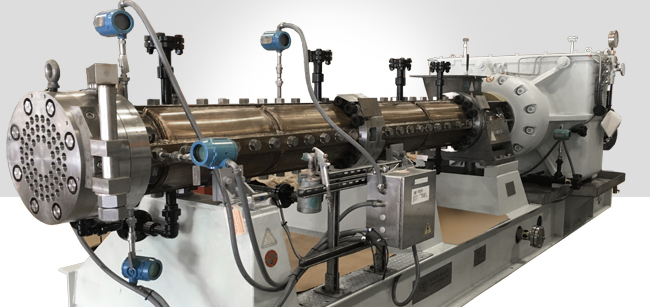
Shown here: Anderson 14A Expander-Dryer
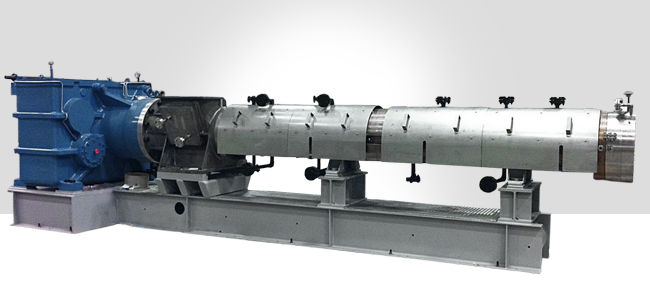
Model | Connected HP | Max Capacity (Kg/Hour) | Moisture Specification |
---|---|---|---|
Model 4-1/2" Expander-Dryer | Up to 100 | 800 | 15 to 8% in, 2% or less out. |
No. 10A/10B Expander-Dryer | Up to 1,800 | 4,000 - 9,000 | 15 to 8% in, 2% or less out. |
No. 14A Expander-Dryer | Up to 2,400 | 10,000-12,000 | 15 to 8% in, 2% or less out. |