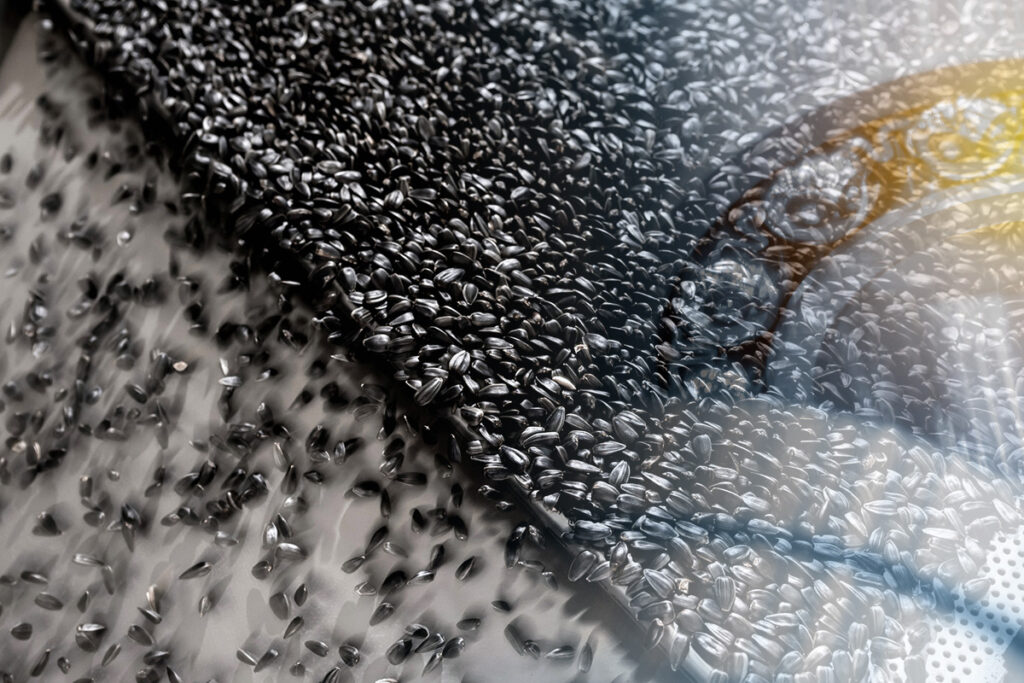
The famous physicist Sir Isaac Newton determined that every action has an equal reaction or opposing force. This law of physics applies to oilseed pressing because as the rotating worm shaft pushes seeds through the barrel, the seeds push back against the shaft, exerting a thrust force in the opposite direction. To absorb this force and keep the shaft rotating smoothly, screw presses depend on thrust bearings to support the load.
This blog will answer a few of the most frequently asked questions about bearings in screw presses.
Let’s take a closer look at the thrust units that keep screw presses spinning.
What is a thrust bearing?
Thrust bearings are like mechanical joints that rotate on stationary braces between machine parts to reduce friction and permit smooth rotation. In a mechanical press, they’re designed to prevent the main worm shaft from drifting by absorbing the load so that the shaft can keep spinning.
These bearings are housed inside thrust units, which may be part of the screw press gearbox, or contained in a separate casing. Either way, these bearings are bathed in oil to lubricate the moving parts and minimize friction to allow smooth rotation.
How thrust bearings work
Essentially, thrust bearings help hold the shaft in place as it rotates, absorbing the thrust force from the oilseeds pushing back against it. Without bearings to absorb this load, the resistance from the seed material could effectively push the shaft back into the gearbox, or at least force it off its center axis to stop it from rotating smoothly.
How to choose the right thrust bearing
To work effectively in any application, bearings must be properly sized to support the load. When sizing bearings, select units built to withstand more force than they’ll likely bear. For example, Anderson International follows a factor of safety of two, meaning that if a screw press exerts 1,000 pounds of thrust force, then the bearings should be rated for 2,000 pounds of thrust load capacity—providing a 2:1 safety net.
Reducing wear-and-tear on bearings
Since these components constantly bear the brunt force of the shaft, they take a lot of abuse. A few events, in particular, can place excessive strain on thrust bearings, so minimizing these can help extend the lifespan of your unit:
- Starting up and shutting down the press causes more unnatural shaft loading than continuous press operation, which can overwork the thrust unit. Limit your use of startups and shutdowns with a preventative maintenance plan for expellers, extruders, and other equipment.
- Interrupting the pressing process by getting a piece of metal or foreign material lodged in the press can suddenly lock up the shaft, generating more force than the thrust unit is designed to handle. Prevent debris from entering your press by cleaning seed material thoroughly before pressing.
- Running the machine in reverse can be detrimental. Operators may attempt to unjam a clogged machine by running it in reverse, like a paper shredder, instead of properly shutting it down and cleaning it out. Thrust bearings are designed to absorb force only from a specific direction, so rotating the shaft backward can destroy the thrust unit and possibly the gearbox along with it.
These three strains can significantly reduce the lifetime of the bearings, whereas a properly maintained unit could easily last five to 10 years before requiring a rebuild. Which brings us to…
Taking care of thrust bearings
While the lubricating oil helps protect the thrust bearings from direct metal-on-metal contact, these parts will naturally wear down over time. Preventative maintenance is critical to keep thrust units at peak performance.
Recommended maintenance procedures for screw press thrust units include:
- Check lubricating oil levels daily and top off if necessary.
- Analyze oil quality monthly to look for metal shavings or other solid particles that could indicate bearing failure.
- Monitor for any unusual noises or vibrations, which may indicate misalignment or worn bearings.
- Change lubricating oil and replace filters at least every 8,000 operating hours.
- Inspect oil seals for leaks or damage at least quarterly, if not more often.
- Monitor the temperature of the lubricating oil continuously, as excessive friction could cause it to overheat. A cooling system can help control oil temperatures.
When it’s time to replace or repair a thrust-bearing unit, Anderson’s technical service team provides rebuilds, replacement parts, repairs, troubleshooting, and maintenance support. We can train your team to carry out repairs or recommended maintenance plans and practices in-house or do it for you.
Beyond mechanical maintenance, ensure your thrust unit is optimized to perform within your processing setup—which requires the shaft and other press parts to work efficiently and demands that seeds are properly pre-treated before pressing. By performing a detailed process audit, Anderson’s application engineer can help optimize your plant’s overall efficiency from the thrust bearings all the way to the oil drainage cage.
Still have more questions about thrust bearings? Contact Anderson today.