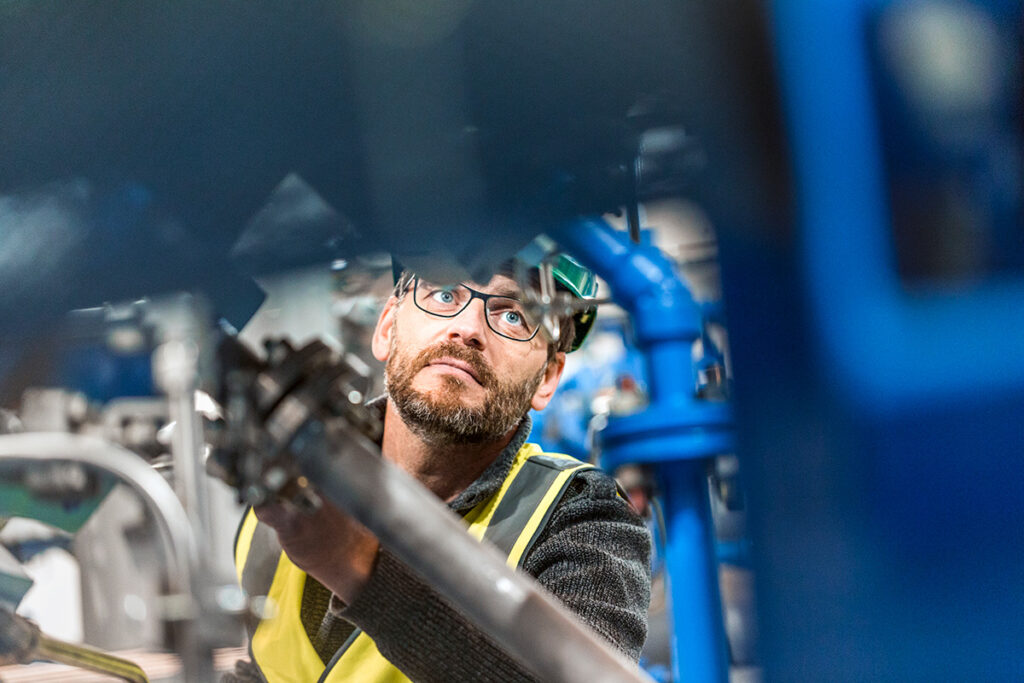
In mechanical oilseed processing plants, the goal of an expeller press is simple: to efficiently crush oilseeds and squeeze out as much oil as possible. But what happens when the machine stops crushing, the oil suddenly stops flowing, or the solids don’t separate completely from the liquids? Suddenly, you’ve hit a processing snag that impacts your oil production—not to mention your profits. Your simple screw press doesn’t seem so simple anymore.
Troubleshooting the most common expeller press malfunctions can save you tons of time and money compared to the costly downtime you’d incur hunting around for the cause of each problem. In this blog, we’ll highlight the most common causes and fixes for nearly any press mishap you’ll encounter.
Diagnosing the most likely causes
Regardless of the specific press setback you’re facing—whether the motor is making weird noises or the machine isn’t running at capacity—most expeller malfunctions can be traced back to one of two leading causes.
- Equipment: The most likely explanation is that the press is worn down. Constant crushing naturally wears down internal parts over time, making the press less effective at compressing. Excessive wear and tear can noticeably impact oil recovery rates and impede the efficient separation of fats from solids.
- Pre-treatment: The other significant factor that impacts press performance is the state of the raw material being crushed. Pre-processing or preparation steps like cleaning, cracking, dehulling, cooking, heating, and drying all play a major role in preparing raw seed for pressing. If the seed entering the press is too wet or dry, too small or big, the expeller will struggle to crush it as efficiently as possible.
For example, suppose an expeller press suddenly stops spinning—a likely culprit is foreign material like screws, stones, or metal scraps that jammed the machine because metal can’t be compressed quite as easily as oilseeds. Those sneaky screws could have entered the press with the seed—pointing to ineffective cleaning upstream—or they could have wiggled themselves loose from inside the barrel—pointing to equipment wear as the cause.
Likewise, if the press is just not producing as much oil as it should, it could be because the internal compression parts are worn out, or maybe because the moisture content of the seed wasn’t in the right range for pressing—which could indicate a problem with the conditioning process, the storage conditions, or the seed itself.
Preventing expeller press malfunctions
Not surprisingly, the two most common fixes to any expeller malfunction you’ll face happen to tie back to the same two causes.
- Since most press mishaps spur from worn or damaged equipment, performing proactive maintenance on a regular schedule is critical. Mechanical processing plants can prevent most press setbacks just by keeping up with expeller press maintenance, replacing worn parts, keeping screws tightened, and lubrication oil topped off.
- Problems stemming from upstream preparation can be addressed by adopting automated control systems to manage each preparation step more consistently—controlling the size, temperature, moisture content, and feed rate of seed entering the press, as well as the amp draw of the motor powering the expeller.
Could the solution to every expeller press problem be as simple as reviewing your pre-treatment processes and scheduled maintenance plan? With so many individual components to inspect inside the press and other steps in the process that can influence its performance, troubleshooting expeller issues may not be as simple as it sounds.
That’s where Anderson International can help with tricky equipment diagnoses, ongoing technical support, machine maintenance, rebuilds, and repairs. In addition to supplying replacement parts and offering a dedicated inventory program, Anderson offers decades of extraction experience and expertise to help processors optimize their entire operation.